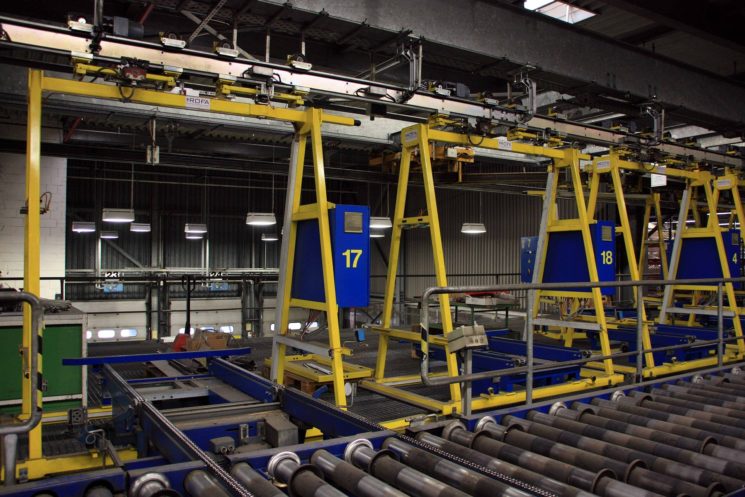
Production equipment and techniques are constantly evolving, but technological advances integrated into the industry do not bring anything concrete if the personnel called upon to implement them do not themselves benefit from improvement programs. The operator remains at the centre of the activity of any organization and its performance levels are still as decisive as ever in terms of the ability of its company to be competitive. The approach called operational excellence is based on this observation. One of its main objectives is to support quality.
Operational excellence: a competitive lever for companies
Optimize productivity and performance, improve production quality and reduce costs. These are the three main objectives of the so-called operational excellence approach.
The promoters of this method see it as a real lever of competitiveness for companies, as all its aspects are organized to move towards performance.
Operational excellence is based on several main axes: customer needs, the ability of operators to think about and implement solutions, and process optimization.
One of the fundamental concepts in the application of operational excellence is collective intelligence, which refers precisely to this idea of staff involvement and motivation. To promote the development of collective intelligence, the role of the proximity manager is central; it is up to him/her to direct, supervise and support operators on different levels (performance, technique, safety, etc.) while serving as a link between the latter and management.
As you will have understood, the operator is the cornerstone of operational excellence. The success of this approach is largely dependent on the company’s human capital policy. It is by empowering its employees to perform well that it can reap the benefits of systematic and methodical reorganization driven by operational excellence.
Improve quality and productivity
As we have seen above, improving product quality is one of the major objectives of operational excellence. In this respect, it is based on principles inherited from systems that have proven their worth in the world of industry, led by Lean Management, the Six Sigma method and their combination, Lean Six Sigma.
The search for efficiency, the reduction of errors, defects and costs, as well as the consideration of customer expectations are characteristic elements of the approach. In this way, it also complies with the foundations of the ISO 9001 standard for quality management.
Operational excellence, therefore, implies making the necessary adjustments to achieve high levels of quality, in particular by improving operators’ processes and working conditions, but it also pursues quantitative objectives that can be measured through a number of indicators.
Here, the reasoning is then done in terms of productivity, time-saving and reduction of the number of defects observed on the products.
About Picomto
Picomto is the web and mobile software solution for creating, managing, sharing, consulting and analyzing visual work instructions.
Leave A Comment