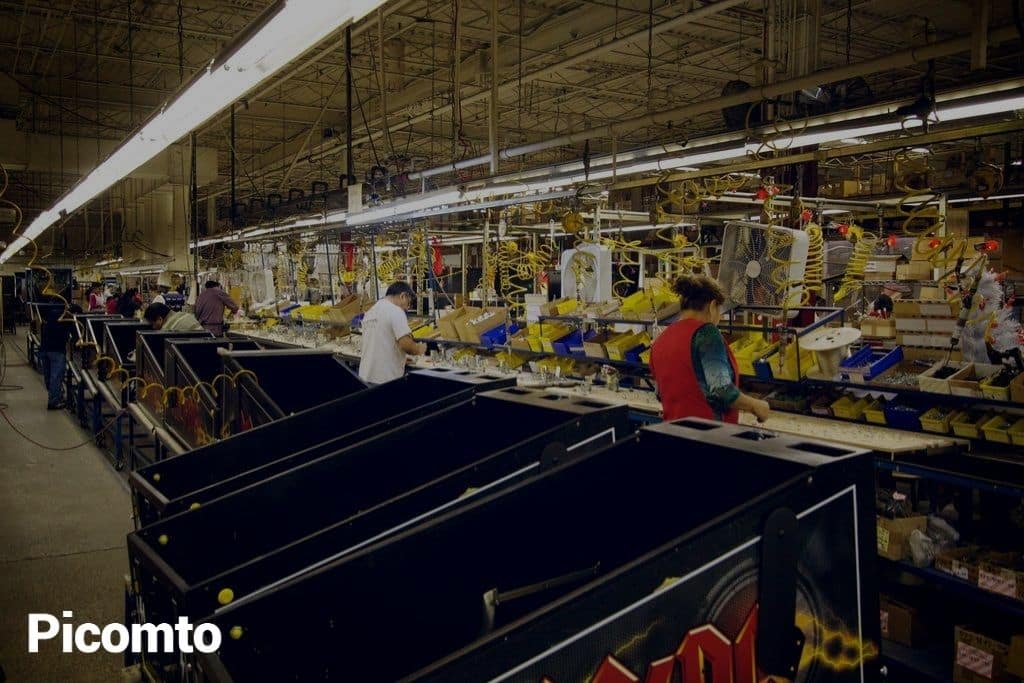
The DMAIC method is used to solve problems in various areas, starting with industry. Combined with the Six Sigma method, it includes 5 steps from defining the problem to evaluating the actions decided and applied to remedy it. Work instructions play a fundamental role in several of these phases; they serve as a reference for the implementation of good practices and are valuable sources of data to be analyzed when improving industrial processes through the so-called DMAIC approach.
DMAIC method: problem-solving and process improvement in 5 steps
DMAIC is an acronym consisting of the initials of the 5 phases that make up this problem-solving approach:
- Define: identify the problem or dysfunction and determine the objectives to be achieved.
- Measure: definition of the variables and indicators to be analyzed, as well as the different tools and methods to be deployed to collect these data.
- Analysis: analysis of the data collected, a precise study of the current situation in relation to the one we want to achieve, the definition of the actions to be implemented.
- Improve: implementation of the action plan thus established for the improvement of the manufacturing process or any other type of process.
- Control: evaluate the efficiency of the action plan, choose the most relevant performance indicators, equip yourself with the tools to modify actions once again if necessary and in order to increase effectiveness.
The importance of work instructions in data collection
As explained above, work instructions are fundamental elements in the application of the DMAIC method steps, especially in the 2nd phase. They are the ones that remind the operator that he must perform measurements at a given point in the value chain and explain how to do so. This allows the DMAIC implementation team to have important data at their disposal and thus to carry out the analysis and then the necessary actions.
Optimization of work instructions as a remedy for the problems identified
Once the problem has been identified, the objective defined and the data analyzed, it will be a matter of reflecting on the solutions, classifying them and making the necessary changes. The latter may very well be directly related to work instructions. Indeed, if sources of slowdown, obstacles to productivity or quality improvement exist in work instructions, it becomes imperative to make corrections.
We are therefore in the 4th phase of the DMAIC method, which is the improvement phase.
Evaluating the effectiveness of changes to work instructions
The effectiveness of the action plan developed as part of a DMAIC project must be evaluated over a given period of time. This is the final step of the method, which makes it possible to verify that the results obtained following its implementation and the optimization of work instructions are in line with the objectives set during the initial phase of the DMAIC method.
Depending on the nature of these objectives (performance indicators, customer satisfaction levels, etc.) and the degree of achievement observed, actions may again be modified to be part of a genuine continuous improvement process.
We are therefore dealing with a cyclical methodology, whose steps are called upon to succeed and repeat themselves in order to constantly strengthen the company’s performance. The application of the DMAIC method implies a regular re-evaluation of work instructions and it is undeniable that this task is facilitated when they are in digital format. From both an organizational and operational point of view, digitized work instructions offer greater possibilities for optimization.
Where can Picomto be involved in the DMAIC method?
Picomto intervenes at several levels on the DMAIC method. With digital work instructions to which visual and other forms are associated, the solution can be used in several of these phases:
- Define: Identify the scope of the problem with interactive diagnostic guides.
- Measure: Collect field data with digital forms integrated into work instructions.
- Analysis: Analyze the collected data to identify pain points and misunderstandings
- Improve: Make recommendations either on the process or on the work instructions (work instructions not detailed enough, the technician does not understand such a step…) and easily upgrade the work instructions by modifying them in 1 click and the technicians access the latest version on their device (smartphone, tablet, computer).
- Control: Ensure that established changes to work instructions and processes are effective, and then eliminate the problem(s).
Feel free to contact one of our experts to find out more. We assist companies in the transformation of their documentation into digital format.
Leave A Comment