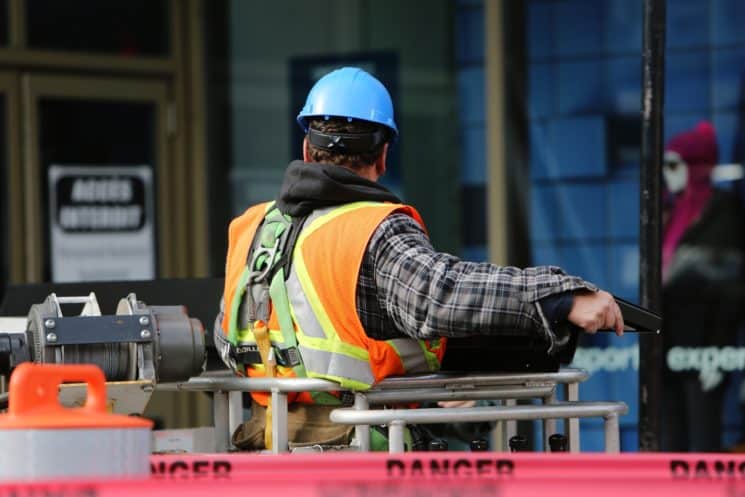
The same way as work instructions, safety measures and verification procedures must be scrupulously observed in order to reduce the risk of incidents that could harm the physical or moral integrity of an employee. Indeed, no organization can neglect the elementary rules of security within its structure. One of the pillars of global management systems is the Occupational Health and Safety Management System (OHSMS), which is as important as the Quality Management System (QMS). The safety approach, which aims to ensure the protection of all industry players against the risks associated with its activity, is a guarantee of the company’s reliability and durability.
Safety procedures are established along the following lines: risk identification, implementation of preventive actions and definition of measures to be applied when a problem arises.
Identify risks
In any safety approach, the first step is generally to define, in the most exhaustive way possible, the various events and dangers that may occur in the context of a given activity. This work is all the more crucial in the world of industry, where all stakeholders operate in an environment that is bound to carry potential dangers. Starting with the operators and technicians, who are in direct contact with the machines and products.
It is on the basis of the information gathered through knowledge of industrial risks that the strategy ensuring the protection of employees will be built. It requires a thorough study of all aspects of the company’s activity. Digital tools provide valuable support in this area by facilitating data collection and analysis.
Implement prevention and intervention measures
Through risk identification work, it is possible to implement a prevention strategy by creating procedures that minimize the likelihood of a hazard occurring. It also makes it possible to organise the interventions to be carried out in the event of an accident.
This strategy cannot be effective if it is not based on collective measures. It also requires the establishment of appropriate infrastructures, such as warning devices and protective equipment, as well as systematic control procedures.
It is also essential that operators and technicians are regularly trained and informed about the risks associated with their work: how to protect themselves from possible pollutants, how to wear as protective equipment in a given area, how to handle machinery without exposing themselves to danger, what instructions to follow to avoid the risk of fire, etc. Otherwise, all the equipment and measures implemented would be completely unnecessary.
To help and guide them, companies apply various tools, including those proposed by ISO 7010, which “prescribes safety signs to be used in accident prevention, firefighting, health risk information and emergency evacuation”. In practice, these are safety and health signs associated with simple and clear pictograms, classified into 5 categories: E for rescue and evacuation signs, F for fire-fighting signs, M for mandatory signs, P for prohibition signs and W for warning signs.
For example, a signal with code P013 corresponds to the prohibition to activate a mobile phone. Code P031 indicates that the switch position should not be changed. The pictogram type E007 indicates an assembly point after evacuation. The danger associated with optical radiation is indicated by the symbol W027.
About Picomto
Today, industry is linked to a strong problem of the transmission of knowledge. The formalization and sharing of knowledge in an industry is crucial for its present and future. Age pyramid, good practices, obligation to follow specific procedures, etc…
Picomto was born from this observation and offers the solution to capture and disseminate the industry’s know-how.
A web and mobile software solution to create, manage, share and analyze maintenance procedures and procedures in a visual and interactive way.
Picomto is part of the digitalization of the industry, #SmartIndustry #Industry4.0, #Paperless
Leave A Comment