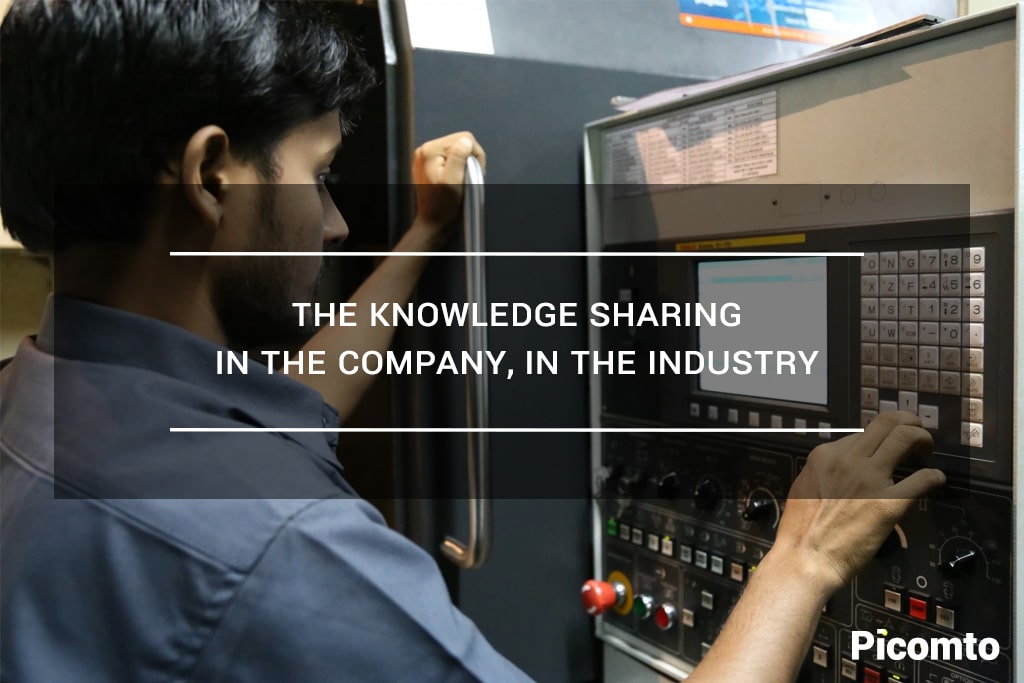
Every company is subject to cyclical movements within its human resources. As employees prepare to retire, newcomers are expected to take over. This raises the problem of knowledge sharing from the first to the second. This transfer of skills between the old and the new generations can only be effectively ensured if it is the subject of a Knowledge Management process.
Knowledge sharing : the stakes
In modern industry, and even in industry 4.0, investing in state-of-the-art equipment and processes is not enough to stay competitive. When we face the departure of experienced employees – retirement requires – and we work to integrate new employees, the risk of a deficit in terms of skills and know-how is very real.
The company can not therefore be content with simple handovers between old and new. It’s a whole organization that needs to be put in place so that valuable skills do not evaporate as teams renew.
Only then can the level of performance and competitiveness of the company be maintained and improved. As a result, the knowledge sharing policy is a key part of the company’s quality system. The ability to achieve quality objectives depends to a large extent on it.
Moreover, it prevents the transfer of undesirable behavior. In other words, it is about establishing the elements of productive know-how to be communicated to new entrants. But also about eliminating conduct that is detrimental to the proper functioning of the company. This prevents recent arrivals from “inheriting” them.
What benefits can we expect?
For newly recruited new employees, it is clear that being accompanied by the elders greatly facilitates their learning. They benefit from a better and faster integration, finding it easier to acquire the necessary knowledge for the job. More than initial training, it is the proximity to experienced employees that allows you to fully understand the work instructions of each position (sequence and sequence of operations).
In addition to technical skills, new entrants also learn about the informal knowledge within the company:
- social and relational codes
- tips
- networks of exchanges
- communication
For their part, their elders also benefit from this process of knowledge sharing as it values their role and their experience. This drives them to continue to invest fully in the life of the company during the rest of their careers.
How to ensure the knowledge sharing?
For the transmission of knowledge to be effective, the company must identify, classify and transfer the important pieces of expertise. But only those that it would really benefit from passing on to new generations of employees. But this must not be done to the detriment of their capacity for autonomy and initiative.
It must also keep abreast of the latest developments in processes, both those directly related to production and those relating, to internal communication. This is one of the main features of Industry 4.0, all aspects of which are affected by digitalization.
The knowledge sharing also makes it necessary to implement a skills’ capitalization plan, which involves identifying the specific knowledge of each position and evaluating their criticality.
This policy is not based on traditional methods such as classroom training and tutoring. It also relies on complementary devices such as companionship, exchange forums or new software solutions.
For example, Picomto is a digital work instruction software used by industrial companies to train newcomers, capitalize and share knowledge within the shop floor. Do not hesitate to contact us to know more about our solution.
Leave A Comment