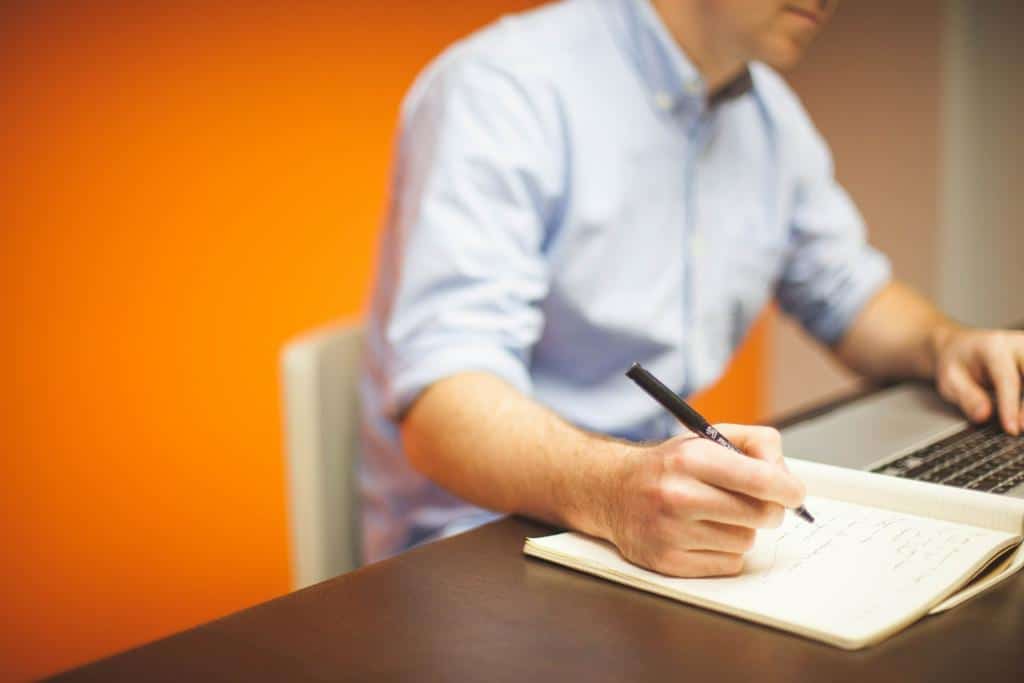
Documentation is one of the pillars of the Quality Management System. The performance and efficiency of the latter therefore depend on it, hence the need to update it. The quality manual and other fundamental documents of the quality system must be constantly updated in order to be a reliable support, aware of developments and able to avoid errors that could affect quality.
The importance of updating quality documentation
Updating quality documentation is crucial in more than one respect. First of all, it is a guarantee that the know-how and knowledge created and acquired by the company will not be lost. To achieve the goals set by the company, it pursues a knowledge management policy by ensuring the identification, analysis, organization, memorization and sharing of knowledge. The systematic updating of documentation, therefore, makes it possible to capitalize on this know-how and transmit it to employees, whether they are newcomers to the company or existing employees who are responsible for replacing others in the event of unavailability (hence greater versatility). New recruits and internal replacements can thus refer to valid documents, effectively guiding them in the performance of their tasks and reducing the risk of error.
In addition, updating quality documents ensures that improvement actions are always in the right direction, that they are not affected by any flaws and that they do not force us to go back.
Finally, the updating of quality documents necessarily has a positive impact on employees’ working conditions and the company’s image. The QHSE (Quality, Health, Safety, Environment) approach – which ensures the safety and health of employees, their training in the prevention, compliance with standards and the reliability of installations – is constantly updated to provide optimal production conditions and improve the customer’s perception of the company. An HSE policy aims to reduce work-related accidents and health problems as well as to affirm the company’s social commitment, particularly with regard to environmental issues.
The different sources of the quality update
The actors involved in updating quality documentation, including the quality manager, of course, rely on different sources to ensure this approach.
First, the updating of quality documents is carried out taking into account customer feedback. Any comments made by the latter after use of the product must be taken into account. They can lead to more or less significant changes in procedures in order to improve product quality and therefore customer satisfaction.
Secondly, audits also make it possible to update quality documents based on observations made during these operations, whether internal or external.
The same applies to the various corrective and preventive actions carried out; these actions must be integrated into existing documents so that the repositories are truly in their latest versions and can be used by stakeholders, without the risk of making mistakes. Moreover, when a correction is made following a given event, the fact of drafting the amendment requires reflection and the implementation of a logical and understandable written structure.
Finally, reviews and revisions are also among the sources of elements to be included in quality documents when they are updated. Management review, for example, can lead to a change in the orientation of company policy (towards more ecological considerations, for example), which leads to changes in procedures, hence the need for updating.
The update, therefore, corresponds to a reactive, dynamic process, which is triggered and determined by the various events affecting the company’s life. It makes it possible, among other things, to have documents that reflect reality and to avoid errors that could affect quality.
About Picomto
Today, the industry is linked to a strong problem of the transmission of knowledge. The formalization and sharing of knowledge in an industry is crucial for its present and future. Age pyramid, good practices, obligation to follow specific procedures, etc…
Picomto was born from this observation and offers the solution to capture and disseminate the industry’s know-how.
A SaaS web and mobile software solution to create, manage, share and analyze operating modes, maintenance procedures, internal procedures, after-sales support.
Picomto is part of the digitalization of the industry, #SmartIndustry #Industry4.0, #Paperless
Leave A Comment