Appartenant au Lean Manufacturing, l’Andon production est un système d’alerte visuelle et auditive installé dans les usines pour signaler les pannes dans la chaîne de production. Ce terme est d’origine japonaise et le système a été utilisé pour la première fois chez Toyota. L’Andon est activable automatiquement ou manuellement pour assurer un meilleur pilotage et une meilleure gestion des arrêts non planifiés. Tout comme la méthode 5S et la méthode Kanban, cela s’inscrit au cœur des notions de résolution de problèmes pour améliorer les processus de production.
Découvrez comment l’Andon peut transformer votre production. Participez à notre webinar pour en savoir plus.
L’Andon production : qu’est ce que le Lean Manufacturing ?
L’Andon production est parti intégrante du Lean Manufacturing. Il est important de bien comprendre la raison d’être de celui-ci pour bien révéler toutes les possibilités des systèmes Andons.
L’approche Lean Digital consiste à éliminer les gaspillages tout au long de la chaîne de production. Il peut s’agir de gaspillage de temps, de stock ou de capacités. Couplé avec les outils d’amélioration continue Kaizen, il permet à l’entreprise de mieux gérer et piloter ses ressources pour une meilleure productivité et assure la performance industrielle.
La philosophie du lean repose sur le concept du Muda, un mot japonais qui signifie « inutile ». Ainsi, en employant les outils Kaizen, le lean consiste à éliminer 8 sources de gaspillage :
- Le temps d’attente du matériel, des décisions ou relatif à la fin de cycle d’une machine. (juste-à-temps)
- Le gaspillage lié au transport de matériel et au transfert d’information.
- Les processus trop compliqués.
- L’espace lié à la conservation des stocks et les ressources impliquées dans sa gestion logistique (gestion des stocks)
- Le mouvement des produits et le déplacement des opérateurs.
- Les produits de mauvaise qualité et les actions nécessaires pour leurs recyclages.
- La surproduction est le pire des gaspillages puisqu’elle implique les 6 autres Muda (flux de production inutile).
- La surqualité, car elle nécessite l’implication de ressources supplémentaires pour dépasser les objectifs fixés.
Plus de détails sur ces gaspillages dans cet article : www.picomto.com/les-8-gaspillages-du-lean-manufacturing/
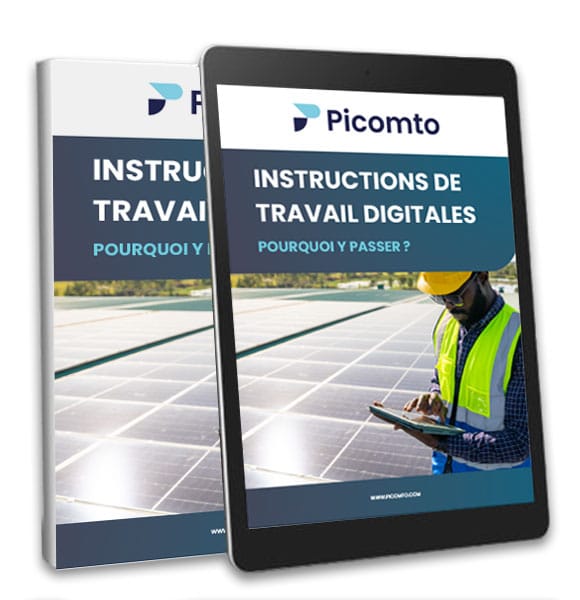
voyages évités chaque semaine
gagnés chaque année
Définition de l’Andon production et mise en place
Très simplement, on peut définir l’Andon comme un outil visuel qui permet d’afficher très simplement une anomalie sur un poste de travail pour ne pas altérer le flux du système de production.
Exemple mis en place avec la solution Picomto chez un client : Un dashboard sur écran est installé sur les lignes de production avec le suivi des opérations en cours. Quand un opérateur rencontre une anomalie, il envoie une alerte via l’instruction de travail digitale qu’il est en train de consulter. L’anomalie s’affiche alors direcrement sur l’écran pour alerter tout le monde.
La création de fiches d’instruction pour les équipes était un processus entièrement manuel. En effet, le contenu était saisi à la main sur un support papier, la mise en page et l’insertion d’éléments visuels se faisaient de manière artisanale. Une fois finalisées, les fiches étaient reproduites en plusieurs exemplaires par photocopie ou impression, puis distribuées physiquement aux techniciens sur le terrain avec un risque de perte. Toute modification du document nécessitait, ainsi, de refaire entièrement la fiche, ce qui rendait la mise à jour fastidieuse. De plus les instructions de travail étaient uniquement basées sur du texte.
Quels sont les différents types d’Andon ?
Les systèmes d’andon sont des outils cruciaux dans le secteur industriel. Ils sont utilisés pour signaler des dysfonctionnements ou des anomalies au sein des processus de production.
Leur objectif principal est d’assurer une communication rapide et efficace entre les opérateurs et les responsables, favorisant ainsi la sécurité, la qualité et l’efficacité. Selon leur mode de déclenchement, les signaux visuels et le niveau d’information fournis, on distingue plusieurs catégories d’andons.
Manuel
L’andon manuel nécessite l’intervention directe de l’opérateur pour signaler un problème. Ce dernier déclenche l’alerte en appuyant sur un bouton ou en tirant sur un cordon.
Le signal visuel se présente souvent sous la forme d’une colonne lumineuse, dont la couleur change pour indiquer l’état du poste (par exemple, vert pour normal et rouge pour un problème). Les informations transmises restent limitées au numéro de poste et à la nature du problème. Cela peut suffire dans des situations où une réaction rapide est indispensable.
Automatique
À l’opposé, l’andon automatique repose sur des capteurs capables de surveiller en continu les paramètres de production.
Lorsqu’une anomalie, comme une fluctuation de température ou de pression, est détectée, le système déclenche l’alerte sans intervention humaine. Le signal visuel peut inclure non seulement une colonne lumineuse, mais aussi un écran fournissant des données chiffrées ou graphiques.
Ce type d’andon offre une information plus complète, facilitant ainsi l’identification rapide des causes de dysfonctionnements et réduisant les temps d’arrêt.
Sonore
L’andon sonore est conçu pour renforcer l’attention des équipes en utilisant des signaux sonores. Parmi ces derniers, nous trouvons : des sirènes, des cloches ou des messages vocaux.
Ce système peut être activé manuellement ou automatiquement, et son intensité peut varier en fonction de la gravité de l’anomalie. La combinaison d’un signal sonore avec un signal visuel améliore l’efficacité de l’alerte. Cela garantit, de ce fait, que chaque membre de l’équipe soit bien informé, même dans des environnements bruyants.
Numérique
L’andon numérique s’appuie sur des technologies de communication avancées pour transmettre des alertes aux personnes concernées, et ce, qu’elles soient présentes sur le site ou non.
Les notifications peuvent être envoyées par SMS, e-mail ou via des applications mobiles. Cela permet d’informer rapidement des responsables qualité, des fournisseurs ou des clients.
Ce type d’andon peut être associé à un signal visuel pour un suivi en temps réel. Cela assure ainsi une réponse rapide et coordonnée face aux problèmes sur le terrain.
Ces différents types d’andons sont essentiels pour optimiser la réactivité et l’efficacité des processus de production. Cela s’effectue en fournissant des alertes adaptées aux besoins variés des opérateurs et des gestionnaires.
Les bénéfices de l’Andon
Le système de management visuel qu’est l’Andon production rapporte de nombreux avantages à l’industrie. En voici quelques-uns :
- Un gain de temps non négligeable : l’affichage visuel des problèmes assure une meilleure compréhension de la situation en réduisant les gaspillages relatifs à la recherche d’informations ou de pannes à cause de l’arrêt de la chaîne de production.
- Une réduction des coûts : parce qu’au sein de l’usine le temps est de l’argent, la réduction du temps perdu permet de réduire les coûts de gestion de production induits par les arrêts non planifiés.
- Une meilleure communication intrinsèque : l’industrie du futur se caractérise par la connectivité des différents acteurs qui échangent les informations et les données en temps réel. Ainsi, l’affichage visuel ou sonore favorise un meilleur flux de communication interne entre les différents intervenants.
- Un meilleur contrôle : en anticipant les problèmes, l’Andon permet aux équipes de maintenance et à la direction d’avoir plus de contrôle sur la chaîne de production.
- La remontée de l’information : afin de développer des systèmes de management efficaces, les informations relatives au fonctionnement de la chaîne de production doivent remonter depuis les plus bas niveaux de la hiérarchie de l’organisation de l’entreprise (postes de travail des opérateurs) vers les postes décisionnels. De cette manière, ces derniers auront une meilleure visibilité et compréhension du fonctionnement de la chaîne de production.
Voyez comment Veolia a réduit ses coûts de production grâce à l’Andon. Consultez notre étude de cas.
Quelles sont les phases de déroulement de l’Andon ?
Un processus Andon typique se déroule en quatre étapes clés :
- Détection : Cette première phase implique l’identification d’un problème, qui peut être effectuée soit par un opérateur (Andon opérateur, Andon approvisionnement), soit par un système automatique (Andon machine). C’est à ce moment que l’alerte Andon est déclenchée.
- Traitement : Une fois l’alerte activée, l’incident est évalué en fonction de sa gravité. À cette étape, il est attribué à la personne ou à l’équipe responsable, comme le manager concerné ou l’équipe de maintenance.
- Visibilité : Dans cette phase, les règles de communication relatives à l’alerte sont mises en œuvre. Cela peut inclure des notifications envoyées directement aux responsables par SMS ou e-mail, ainsi que des affichages collectifs dans l’atelier pour informer l’ensemble de l’équipe.
- Amélioration : Après la résolution de l’incident, les détails sont enregistrés dans une base de données. Ces informations sont précieuses pour les équipes qui travaillent à l’anticipation et à la résolution proactive des incidents récurrents ou critiques à l’avenir.
Ces étapes permettent d’assurer une gestion efficace des problèmes, contribuant ainsi à l’amélioration continue du processus de production.
Comment utiliser l’Andon efficacement ?
L’andon n’est pas nécessairement adapté à tous les processus de production. Il est essentiel d’identifier les situations propices à son utilisation en tenant compte des spécificités du processus et des objectifs à atteindre.
Voici quelques critères à considérer pour évaluer la pertinence de l’andon dans votre environnement de travail :
- Complexité du processus : Plus un processus est complexe, plus il est susceptible de rencontrer des problèmes. Dans ce cas, l’andon peut faciliter la communication et la coordination entre les différents intervenants, contribuant ainsi à une gestion plus efficace des incidents.
- Fréquence des problèmes : Si un processus est souvent confronté à des problèmes récurrents, il devient crucial de les signaler et de les résoudre rapidement. L’andon peut alors jouer un rôle clé dans la réduction des temps d’arrêt et des coûts liés à ces interruptions.
- Criticité des problèmes : Les problèmes ayant un impact significatif sur la qualité du produit ou la satisfaction du client doivent être traités en priorité. L’andon peut être un outil précieux pour prévenir ou corriger ces problèmes de manière immédiate, contribuant ainsi à améliorer la qualité des produits et à renforcer la satisfaction client.
- Variabilité du processus : Les processus soumis à des variations, qu’elles soient internes ou externes (comme des fluctuations de demande ou des changements de ressources), peuvent être difficiles à contrôler. L’andon peut aider à détecter rapidement les écarts et à ajuster le processus pour maintenir la performance souhaitée.
- Standardisation du processus : Un processus bien standardisé, qui suit des règles et des procédures claires, facilite la définition des conditions normales et anormales.
L’andon peut alors être utilisé pour s’assurer que les standards de travail sont respectés et pour favoriser une amélioration continue.
En prenant en compte ces critères, vous pourrez maximiser l’efficacité de l’andon dans votre processus de production, en veillant à ce qu’il soit utilisé de manière judicieuse et bénéfique.
Trois conseils pour mettre en œuvre le système Andon
Une fois que vous avez identifié les opportunités d’utiliser le système Andon, il est crucial de mettre en place le type d’alerte visuelle le plus adapté à votre processus de production.
Pour assurer une mise en œuvre efficace, nous vous conseillons de :
- Choisir le type approprié : Selon le mode de déclenchement de l’alerte, le type de signal visuel et le niveau d’information requis, il est possible de sélectionner un andon manuel, automatique, sonore ou numérique. En fonction des besoins spécifiques de votre environnement, vous pouvez également envisager de combiner plusieurs types pour renforcer l’efficience du système.
- Déterminer les couleurs et les sons adéquats : Il est essentiel d’utiliser des couleurs et des sons différents pour signaler la nature et l’urgence des problèmes. Par exemple, le rouge peut signaler un arrêt critique, le jaune une alerte, le vert un fonctionnement normal, et le bleu une demande de maintenance. De plus, des sons variés, modulés en fréquence ou en intensité, peuvent indiquer différents niveaux de gravité, attirant ainsi l’attention des opérateurs de manière ciblée.
- Sélectionner l’emplacement optimal : Le placement de l’andon doit être stratégique. Selon la taille et la configuration de votre site de production, il peut être installé au-dessus des postes de travail, sur un mur ou sur un écran. L’objectif est de garantir que l’andon soit visible par tous les intervenants, y compris le chef d’équipe, le responsable de production et le service de maintenance. Pour améliorer la visibilité, vous pouvez également utiliser des miroirs ou des caméras.
- Former les opérateurs à son utilisation : Il est fondamental de former les opérateurs sur le fonctionnement, l’importance et les règles d’utilisation de l’andon. Ils doivent comprendre comment déclencher une alerte, interpréter les signaux visuels et sonores, réagir face à un problème et confirmer sa résolution. Il est également important de leur faire comprendre que l’utilisation de l’andon est un outil d’amélioration et non une sanction.
- Suivre et analyser les données : Une collecte et une analyse régulières des données générées par l’andon sont cruciales pour évaluer son efficacité. Cela permet d’identifier les causes profondes des problèmes et de mettre en place des mesures correctives ou préventives. Vous pouvez suivre des indicateurs tels que le nombre d’alertes déclenchées, la durée moyenne des arrêts et le taux de résolution des problèmes. Des outils d’analyse comme le diagramme d’Ishikawa ou la méthode des 5 pourquoi peuvent également être utiles pour explorer les causes des problèmes.
En suivant ces conseils, vous pourrez mettre en place un système Andon efficace qui contribuera à améliorer la performance de votre processus de production
Exemple d’Andon lean : Toyota
Il faut dire qu’observer le fonctionnement d’un système Andon en action permet de mieux comprendre son efficacité. Toyota est souvent cité en exemple pour sa mise en œuvre exemplaire de ce principe. Voici un aperçu concret de son application sur le terrain :
Chez Toyota, le système Andon agit comme un mécanisme d’alerte qui peut entraîner l’arrêt temporaire de la ligne de production.
Lorsqu’un problème est identifié, un opérateur peut tirer sur un cordon qui déclenche une alarme sonore, accompagnée d’un tableau lumineux. Ce tableau signale immédiatement aux responsables d’équipe qu’un problème a été détecté sur une ligne de production spécifique.
Si le problème ne peut pas être résolu rapidement, la ligne s’arrête pour éviter toute dégradation de la qualité.
Chaque employé a le pouvoir d’interrompre la chaîne de production s’il estime qu’il y a une menace pour la qualité du véhicule. Cela souligne l’engagement de Toyota envers l’amélioration continue et la qualité.
Cas d’utilisation de l’Andon dans une production
Pour illustrer le fonctionnement d’un système Andon, considérons une ligne de production composée de plusieurs postes de travail.
Chaque poste est équipé d’un bouton ou d’un cordon Andon, relié à une colonne lumineuse positionnée au-dessus.
Cette colonne peut afficher différentes couleurs en fonction de l’état du poste :
- vert (normal),
- jaune (alerte),
- rouge (arrêt)
- et bleu (maintenance)
Elle est également connectée à un tableau de bord central qui indique le numéro du poste ayant déclenché l’alerte, ainsi que le type et la durée du problème.
Imaginons qu’un opérateur découvre un défaut sur une pièce qu’il vient de produire. Il actionne alors le bouton Andon, ce qui allume la colonne lumineuse en rouge et arrête la ligne de production.
Sur le tableau de bord central, le numéro du poste, la nature du problème (qualité) et le temps écoulé depuis l’alerte sont affichés. Le chef d’équipe, qui supervise la production, se rend immédiatement au poste concerné pour analyser la cause du défaut et assister l’opérateur dans la résolution du problème.
Si la situation est rapidement corrigée, l’opérateur presse de nouveau le bouton Andon, ce qui éteint la colonne lumineuse et redémarre la ligne de production.
En revanche, si le problème nécessite l’intervention du service de maintenance, l’opérateur utilise un autre bouton. Cela allume la colonne lumineuse en bleu et envoyant une notification au service de maintenance. Ce dernier se dirige alors vers le poste pour effectuer les réparations nécessaires.
Une fois le problème résolu, le personnel de maintenance appuie sur le bouton, éteignant la colonne lumineuse et relançant la production.
Utilisation d’un système Andon numérique dans un environnement de production moderne
Avec l’émergence de l’industrie 4.0, de nombreuses entreprises adoptent une version numérique du système Andon. Ce système ou logiciel Andon numérisé utilise l’interconnectivité entre les machines sur le terrain et les systèmes distants pour détecter automatiquement les problèmes durant le processus de production. Il envoie des notifications instantanées aux opérateurs, superviseurs et équipes de maintenance concernées.
De plus, le tableau Andon moderne offre une vue précise et en temps réel de l’état de la production, permettant aux opérateurs et superviseurs de suivre :
- les objectifs,
- les performances
- et les temps d’arrêt
Cela garantit, ainsi, une visibilité constante sur les opérations de l’usine.
Améliorez continuellement vos opérations avec l’Andon et la digitalisation.
Contactez nos experts pour en savoir plus.
Andon production et Instructions de Travail Digitales
Il est évident de dire que l’Andon a une place indispensable au sein de l’industrie connectée. Couplé avec des instructions de travail digitales, les opérateurs ont désormais tous les outils pour améliorer leur productivité et efficacité et optimiser la production. Cela permet, ainsi, de garantir l’efficacité opérationnelle.
Picomto est le leader européen des solutions d’instructions de travail digitales à destination des entreprises industrielles. Réservez votre démonstration à remplissant ce formulaire.
Associez l’Andon à des instructions de travail digitales pour une productivité maximale. Réservez une démonstration de notre solution.
Conclusion
En conclusion, le système Andon se révèle être un outil précieux pour optimiser les processus de production. Il permet de détecter rapidement les anomalies, d’améliorer la communication entre les équipes et de réduire les temps d’arrêt. En favorisant une culture de l’amélioration continue, l’Andon contribue à une hausse de la productivité et de la qualité des produits.
Pour une mise en œuvre réussie, il est essentiel de choisir le type d’Andon adapté à ses besoins, de former les équipes et de suivre régulièrement les performances du système.
FAQ
Comment fonctionne Andon ?
Le système Andon permet aux opérateurs de signaler des problèmes en temps réel en utilisant un bouton ou un cordon. Cela active une colonne lumineuse qui indique l’état du poste via des couleurs (normal, alerte, arrêt, maintenance) et affiche des informations sur un tableau de bord central, facilitant une réponse rapide aux problèmes.
Qu’est-ce qu’une carte Andon ?
Une carte Andon est un outil visuel affichant des informations essentielles sur les alertes en cours, comme le numéro du poste et le type de problème. Elle aide les équipes à suivre l’état des opérations et à prioriser les interventions.
Qui a inventé le cordon Andon ?
Le cordon Andon a été popularisé par Toyota dans le cadre de son système de production lean. Il permet aux opérateurs d’arrêter la ligne de production en cas de problème, favorisant ainsi la qualité et l’amélioration continue.
À quoi servent les lampes Andon ?
Les lampes Andon, ou colonnes lumineuses, signalent l’état des postes de travail. Elles utilisent des couleurs différentes pour indiquer le fonctionnement normal (vert), une alerte (jaune), un arrêt (rouge) ou une demande de maintenance (bleu), facilitant ainsi une communication rapide sur le statut de la production.
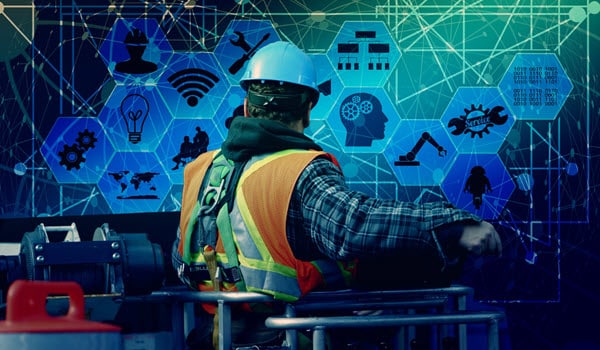
Laisser un commentaire