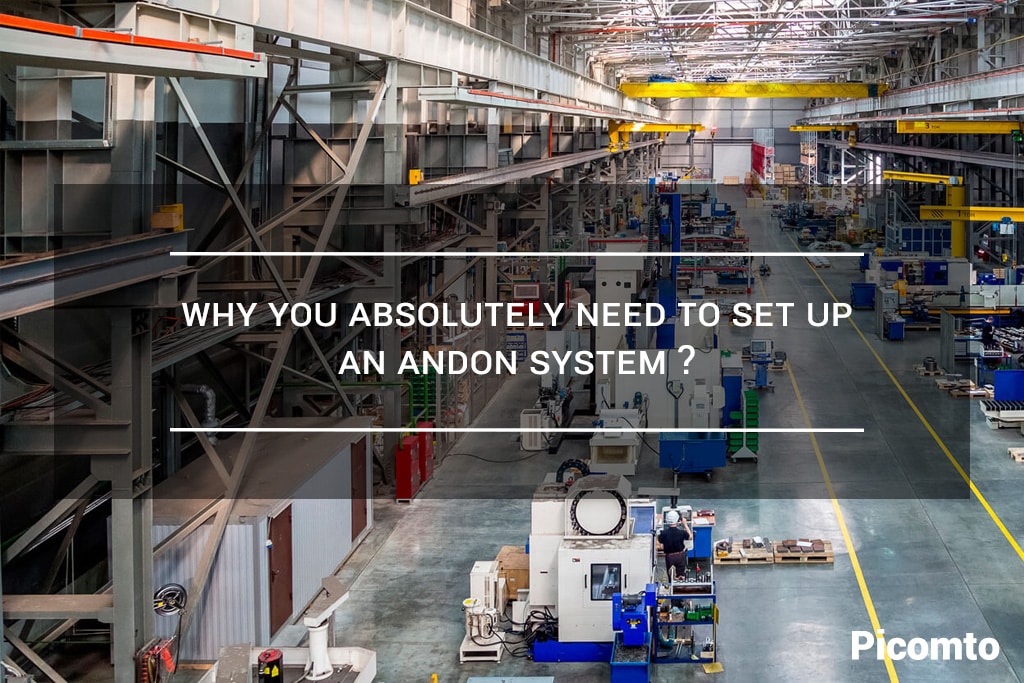
Belonging to Lean Manufacturing, Andon is a visual and audible alert system installed in factories to signal failures and inefficiencies in the production chain. It is a coined term of Japanese origin and the system was used for the first time at Toyota. The Andon can be activated automatically or manually to improve efficiency and ensure better management of production downtimes.
Lean Manufacturing: what is it?
Andon is part of Lean Manufacturing processes. It is important to understand the reason for it to fully reveal all the possibilities of the Andon systems.
Lean Manufacturing is about eliminating waste all along the production line. It can be a waste of time, stock or capacity. Coupled with Kaizen tools and techniques, it allows the company to better manage its resources for better productivity.
The Lean philosophy is based on the concept of Muda, a Japanese word meaning “useless”. This way, the utilization of Kaizen tools, Lean is about eliminating 7 sources of waste:
- Transportation: The waste associated with the transportation of equipment and the transfer of information.
- Inventory: The space related to the conservation of the stock and the resources involved in its management.
- Motion: The movement of products and the movement of operators.
- Waiting: The waiting time of the equipment, decisions or the end of the machine cycle.
- Overprocessing: The processes too complicated.
- Overproduction: It is the worst waste because it involves the other Muda.
- Defects: Poor quality and defective products and the actions necessary for their recycling.
Definition of Andon and setting up:
Very simply, we can define the Andon as a visual tool that can easily display an anomaly or defects on a workstation.
An example set up with the Picomto solution at a customer:
An on-screen dashboard is installed on the production lines with the monitoring of the operations in progress. When an operator encounters an anomaly, he sends an alert via the digital work instruction he is viewing. The anomaly is then displayed directly on the screen to alert everyone.
Benefits of Andon
The visual management system that is Andon brings many measurable benefits to the industry. Here are a few :
- Significant time savings: the visual display of problems provides a better understanding of the situation by reducing and minimizing the waste involved in finding information or breakdowns involved in the shutdown of the production line.
- Cost reduction: because in the factory time is money, time reduction can reduce production costs caused by unplanned downtime and that would ensure profitability.
- Better communication: the industry of the future is characterized by the connectivity of the different actors who exchange information and data smoothly in real-time. Thus, the visual or sound display promotes a better flow of internal communication between the various stakeholders, practitioners, facilitators and supervisors.
- Better control: By anticipating and forecasting problems, Andon allows maintenance teams and management to have more control over the production chain.
- Information collection: in order to develop and sustain effective management systems, information about the functioning of the production chain must go from the lowest levels of the organization’s hierarchy to decision-making positions. In this way, they will have better visibility and understanding of the functioning of the production chain.
Continuous improvement and operational excellence
Operational excellence brings together all the procedures for continuous improvement. That is lean management. What is lean? It is the theory Of Constraints (TOC), agile methods and personal development. In fact, it aims to improve the well-being of the different actors in the plant and the working conditions. in order to achieve high-level performance.
Andon is at the heart of Kaizen continuous improvement approach because it opens the door to various continuous improvement approaches that aim to optimize the plant’s performance at all levels.
Andon and Digital Work Instructions
It is obvious to say that Andon has an crucial place in the connected industry. Coupled with digital work instructions, operators now have all the tools to improve their productivity and efficiency.
Picomto is the European leader in digital work instruction solutions for industrial companies. Belonging to Lean Manufacturing, Andon is a visual and audible alert system installed in factories to signal failures in the production chain. This term is of Japanese origin and the system was used for the first time at Toyota. The Andon can be activated automatically or manually to ensure better management of production downtimes.
Leave A Comment