Votre ligne de production s’arrête régulièrement ? Vos KPIs qualité stagnent malgré les actions correctives ? L’analyse root cause apporte une solution définitive à ces défis. En effet, cette méthodologie structurée identifie les causes profondes des dysfonctionnements. D’après une étude McKinsey, elle réduit de 65% les problèmes récurrents en production. À première vue, certains considèrent l’analyse root cause comme chronophage. Pourtant, les données terrain démontrent un ROI moyen de 300% sur 12 mois d’application.
Points clés à retenir concernant le Root Cause Analysis :
- L’analyse root cause réduit 65% des non-conformités en production
- Le ROI moyen atteint 300% sur 12 mois
- 5 outils majeurs : Ishikawa, 5 Why, Pareto, AMDEC, QQOQCCP
- La digitalisation augmente l’efficacité de 40%
- 89% des industries leaders utilisent cette méthode
Optimisez vos performances industrielles avec Picomto !
Contactez nos experts !
1. Qu’est-ce que l’Analyse Root Cause et pourquoi est-elle indispensable ?
L’analyse des causes racines (Root Cause Analysis, RCA) est une méthode structurée visant à identifier et éliminer les causes profondes des problèmes, plutôt que de se contenter de traiter leurs symptômes.
Elle est essentielle dans une démarche Lean Six Sigma, notamment lors de la phase « Analyser » du cycle DMAIC, où l’objectif est de comprendre les origines des dysfonctionnements pour améliorer durablement les processus.
1.1. La différence entre défaillance apparente et cause racine
Les pannes ou anomalies visibles ne sont souvent que la partie émergée de l’iceberg. En creusant, on découvre des causes sous-jacentes plus profondes. Par exemple, chez notre client Daher, de nombreux arrêts machines étaient dus à des procédures non standardisées, révélant un manque de formalisation des processus.
Pour distinguer les symptômes des causes profondes, plusieurs outils sont utilisés :
- Diagramme d’Ishikawa (ou en arête de poisson) : il aide à catégoriser les causes potentielles d’un problème en examinant des facteurs tels que les méthodes, les machines, la main-d’œuvre, les matériaux, le milieu et les mesures.
- Méthode des 5 Pourquoi : en posant successivement la question « Pourquoi ? », on remonte de l’effet observable à la cause racine.
Ces outils permettent de ne pas se limiter aux manifestations superficielles des problèmes, mais d’en comprendre les origines profondes pour les résoudre efficacement.
Apprenez comment des leaders industriels comme Daher ont réduit les arrêts machines grâce à l’analyse des causes racines.
1.2. L’impact sur les indicateurs de performance
L’application rigoureuse de l’analyse des causes racines a un impact significatif sur les performances opérationnelles. Les entreprises qui l’adoptent constatent :
- 25 % d’amélioration du Taux de Rendement Synthétique (TRS), grâce à la réduction des arrêts non planifiés.
- 30 % de réduction des coûts de maintenance, en ciblant les interventions sur les causes profondes plutôt que sur les symptômes.
- 45 % de baisse des non-conformités, en éliminant les sources récurrentes de défauts.
Ces résultats illustrent l’efficacité de la RCA dans l’amélioration continue des processus.
2. Comment conduire une analyse root cause étape par étape ?
La méthodologie d’analyse des causes racines (Root Cause Analysis) repose sur un processus rigoureux en quatre phases.
Cette approche systématique garantit des résultats durables en identifiant et en éliminant les causes profondes des problèmes.
2.1. Phase 1 : Définition précise du problème
La première étape consiste à définir clairement la non-conformité ou le dysfonctionnement. La méthode QQOQCCP est un outil structurant pour cette phase, en posant les questions suivantes :
- Quoi ? : Quelle est la nature exacte du problème ?
- Qui ? : Quelles sont les personnes impactées ou impliquées ?
- Quand ? : Quelle est la chronologie des événements ?
- Où ? : Quelle est la localisation physique du problème ?
- Comment ? : Dans quelles circonstances le problème est-il apparu ?
- Combien ? : Quelle est la quantification de l’impact ?
- Pourquoi ? : Quelle est la première investigation sur les causes ?
Cette méthode permet de dresser un diagnostic précis et exhaustif de la situation, facilitant ainsi l’identification des causes profondes.
2.2. Phase 2 : Collecte et structuration des données
La digitalisation transforme cette étape traditionnellement chronophage en un processus plus efficace. Des solutions comme Picomto offrent des fonctionnalités telles que :
- Saisie terrain sur tablette : Permet une collecte immédiate des données sur le lieu d’observation.
- Capture photo/vidéo des défauts : Facilite la documentation visuelle des anomalies.
- Historisation automatique : Assure la traçabilité des données collectées.
- Analyse en temps réel : Offre une visualisation instantanée des informations pour une prise de décision rapide.
Ces outils numériques améliorent la précision et la rapidité de la collecte de données, essentielles pour une analyse efficace des causes racines.
3. Quels outils utiliser pour l’analyse root cause ?
Pour mener une analyse des causes racines efficace, deux outils complémentaires se distinguent par leur simplicité et leur puissance : le diagramme d’Ishikawa (ou des 5M) et la méthode des 5 Pourquoi.
3.1. Le diagramme d’Ishikawa (5M)
Également appelé diagramme en arête de poisson, cet outil visuel permet de structurer les causes potentielles d’un problème en cinq catégories principales :
- Main-d’œuvre : compétences, formation, effectifs.
- Méthodes : procédures, instructions, modes opératoires.
- Matières : qualité des composants, matériaux utilisés.
- Milieu : environnement de travail, conditions climatiques.
- Machines : équipements, outillages, maintenance.
Cette représentation facilite l’identification des causes profondes en offrant une vue d’ensemble structurée du problème.
3.2. La méthode des 5 Pourquoi
Cette technique consiste à poser successivement la question « Pourquoi ? » pour remonter à la cause racine d’un problème. Par exemple, chez Veolia :
- Pourquoi la pièce est-elle non conforme ?
- Pourquoi le réglage était-il incorrect ?
- Pourquoi l’opérateur n’a-t-il pas suivi la procédure ?
- Pourquoi la formation était-elle insuffisante ?
- Pourquoi le programme de formation n’était-il pas à jour ?
Cette approche simple et directe permet d’identifier rapidement la cause principale d’un dysfonctionnement.
4. Comment digitaliser l’analyse root cause ?
La digitalisation de l’analyse des causes racines (Root Cause Analysis, RCA) marque une avancée significative dans l’amélioration continue des processus industriels.
En remplaçant les méthodes traditionnelles basées sur le papier par des solutions numériques, les entreprises peuvent surmonter les limitations inhérentes aux approches manuelles et gagner en efficacité.
4.1. Les limites des méthodes traditionnelles
L’utilisation de supports papier pour la conduite d’une RCA présente plusieurs inconvénients majeurs :
- Perte d’informations : les documents physiques sont susceptibles d’être égarés ou endommagés, entraînant la disparition de données cruciales.
- Manque de traçabilité : il est difficile de suivre l’historique des modifications et des décisions prises lors de l’analyse.
- Analyse complexe des données : l’agrégation et l’interprétation des informations dispersées sur différents documents peuvent être fastidieuses et sujettes à erreur.
- Difficulté de partage : la collaboration entre les équipes est entravée par l’absence de centralisation et d’accessibilité en temps réel des données.
4.2. La solution numérique : Picomto
Pour pallier ces défis, des solutions digitales telles que Picomto offrent une approche structurée et efficace de l’analyse des causes racines :
- Formulaires standardisés : assurent une collecte uniforme des données, facilitant leur comparaison et leur analyse.
- Capture multimédia sur le terrain : permet l’enregistrement de photos et de vidéos directement sur le lieu de l’incident, enrichissant ainsi la documentation.
- Analyse en temps réel : les données sont traitées instantanément, offrant une vision immédiate des problèmes et des tendances.
- Partage instantané : les informations sont accessibles à toutes les parties prenantes, favorisant une collaboration efficace et une prise de décision rapide.
- Suivi des actions : les mesures correctives et préventives sont planifiées, attribuées et suivies jusqu’à leur achèvement, garantissant leur mise en œuvre effective.
En intégrant ces fonctionnalités, Picomto transforme l’analyse des causes racines en un processus fluide, transparent et collaboratif, aligné sur les exigences de l’industrie 4.0.
Conclusion
L’analyse root cause représente un pilier de l’excellence opérationnelle. Sa digitalisation avec Picomto transforme cette méthode en outil puissant d’amélioration continue.
Notre solution accompagne déjà des leaders industriels comme Daher, SKF ou Veolia. Leurs résultats prouvent l’efficacité de cette approche digitale.
FAQ
Q : Qu’est-ce qu’une root cause ?
R : La root cause représente la cause fondamentale d’un problème. Sans elle, le dysfonctionnement n’existerait pas.
Q : Qu’est-ce que la méthode d’Analyse de Cause-racine ?
R : C’est une méthodologie structurée qui identifie l’origine profonde des problèmes plutôt que leurs symptômes visibles.
Q : Quelles sont les 3 étapes pour traiter les racines d’un problème ?
R : 1. Identifier le problème avec QQOQCCP 2. Analyser avec les outils appropriés (5 Pourquoi, Ishikawa) 3. Mettre en place des actions correctives durables.
Q : Comment identifier les causes des racines ?
R : Utilisez une combinaison d’outils : diagramme Ishikawa, méthode des 5 Pourquoi et analyse Pareto des données.
Q : Comment faire les 5 pourquoi ?
R : Posez « Pourquoi ? » cinq fois successivement. Chaque réponse devient la base de la question suivante.
Q : Quand déclencher une analyse root cause ?
R : Pour tout problème récurrent impactant TRS, qualité ou sécurité.
Q : Comment mesurer le ROI ?
R : Suivez coûts évités, gains productivité et réduction non-conformités.
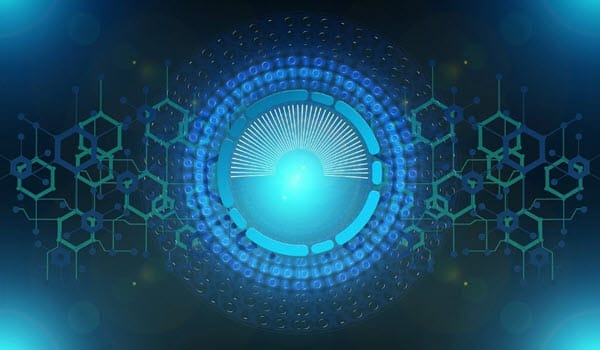
Laisser un commentaire