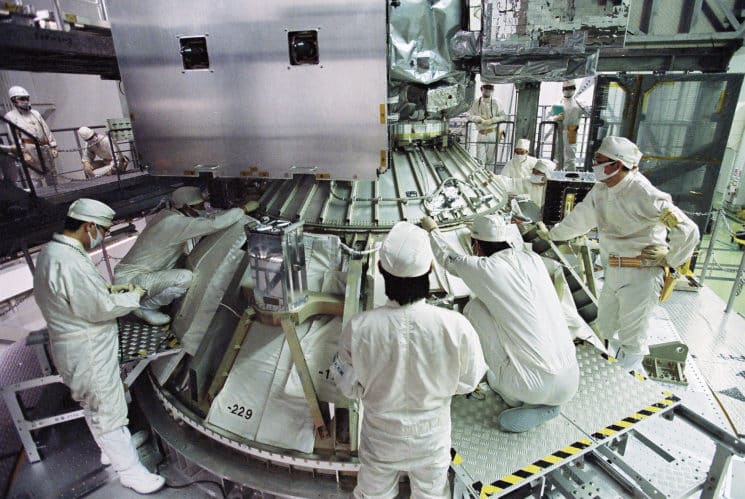
No company can aim to remain efficient and therefore competitive without giving itself the means to constantly improve. Faced with competition, constantly improving its production in terms of both quality and quantity is the key to staying afloat and not being overtaken. Different methods can be used to achieve this objective. One of them is to improve standard operating procedures (SOP) by applying Lean principles.
Standardization to reduce productivity barriers
SOP are certainly not the only aspect on which manufacturers are required to focus their improvement efforts, but they are undoubtedly one of the priorities.
The reason is simple: operating methods are really the heart of production. These are the “recipes” to be followed to achieve from an initial state to a final state of a product. The quality of the latter therefore depends greatly on it.
However, any activity in the industry is likely to have snags, elements that are enemies of quality and performance: muda (waste), muri (excess) and mura (variability).
The aim is therefore to work to protect standard operating procedures from these undesirable factors. One of the tools used for this purpose and part of the Lean manufacturing concepts is the standardisation of work instructions. It is certainly not the most recent of the principles, but it remains a sure value when it comes to guiding employees with a support that describes in detail the operations to be carried out. This reduces the risk of errors and, when these procedures are optimized, so are the sources of waste, excess and time wasted.
Focus on digital media
The media mentioned above tend to evolve themselves to allow industry players to contribute, each at its own level, to improve the overall performance of their organization.
Today, paper documents are gradually disappearing in favour of digital platforms that offer greater ease of use, considerable time savings, and increased sharing and transmission possibilities. An evolution towards paperless, which also concerns SOP; work instructions are made available to operators on terminals that they have permanently on them or nearby and which are accessible to them with a few clicks or keys. The digitisation of work instructions is therefore at the service of efficiency, as recommended by the Lean methodology.
Gradual but constant improvements
Rather than rethinking everything and opting for radical changes (breakthrough innovations also called Kaikaku), Lean manufacturing encourages improvement in small but continuous doses. A principle that reflects the Kaizen spirit and has the advantage of being generally better perceived by employees, who thus have time to adapt to changes in procedures. Indeed, applying excessive and abrupt changes to work instructions runs the risk of developing difficulties or even reticence, which obviously does neither productivity nor quality any good.
Gradual improvements are also encouraged because they often result from the contribution of field staff themselves, through observations and suggestions that they can make through their knowledge of their working environment. Being in daily contact with the machines and applying the work instructions, they are ideally placed to identify any shortcomings and identify improvements to be made.
The involvement of all the company’s stakeholders, without exception, is one of the keys to operational excellence and performance in the industry. This is the essence of the Lean methodology and its application to SOP.
Picomto is the European leading digital work instructions software solution. Contact us to know more.
Leave A Comment