Is your company looking to reduce maintenance costs while improving equipment reliability? Do you want to minimize machine downtime and boost productivity? First-level maintenance is the ideal solution.
Accessible, efficient, and structured, it enables companies to save up to 30% on maintenance costs while preventing breakdowns.
Moreover, when combined with technologies for remote maintenance of industrial machines, it offers an even greater capacity to respond rapidly to anomalies without requiring on-site interventions.
It also plays a key role in improving industrial machine durability by promoting consistent upkeep and early issue detection.
In this comprehensive guide, discover how to implement, optimize, and digitize it to turn it into a true industrial performance driver
Key Takeaways
- First-level maintenance is the foundation of any effective maintenance strategy.
- It reduces overall maintenance costs by up to 30%.
- It can be carried out by operators after basic training.
- Digitalization improves its efficiency by 40%.
- It helps reduce machine downtime by 25%.
1. What Is First-Level Maintenance and Why Is It Essential?
First-level maintenance is the first line of defense against industrial breakdowns. It includes all simple and regular interventions performed directly at the workstation.
Its goal? Ensure the proper functioning of equipment, reduce production downtime, and extend machine lifespan.
1.1. Definition and Key Role of First-Level Maintenance
At first glance, this type of maintenance may seem basic. However, it plays a crucial role in preventive maintenance strategies.
According to recent studies, it accounts for 45% of maintenance actions in the industrial sector, underscoring its importance.
The tasks involved are simple yet essential:
- Cleaning components to prevent dust and residue buildup.
- Lubricating moving parts to reduce wear and friction.
- Conducting visual inspections to quickly detect potential anomalies.
These actions help prevent malfunctions and improve machine reliability. A compelling example is SKF: by integrating these practices, the company reduced breakdowns by 35%.
1.2. A Cornerstone of Maintenance Strategy
First-level maintenance follows a structured approach. It forms the fundamental base of a five-level hierarchy, where it plays a key role in failure prevention.
Its effectiveness relies on:
- Operator involvement: Production teams carry out these tasks themselves, ensuring faster response times.
- Integration into the overall maintenance plan: It complements corrective and predictive maintenance by addressing issues before they escalate.
- Direct impact on industrial performance: Regular interventions lower repair costs and increase equipment availability.
When properly implemented, first-level maintenance enhances efficiency, productivity, and safety.
Looking to optimize your strategy ? Discover our tailored solutions!
2. What Are the Concrete Benefits of First-Level Maintenance?
Adopting a well-structured first-level maintenance approach is a step toward more reliable and efficient production.
The benefits are immediate and measurable. Companies using Picomto report an average 40% reduction in machine downtime. Fewer breakdowns mean greater availability and, ultimately, improved profitability!
2.1. A Powerful Lever to Reduce Production Costs
Properly anticipated maintenance leads to substantial cost savings. According to a Deloitte study, an effective first-level maintenance strategy can:
- Reduce maintenance costs by 30% by minimizing major repairs.
- Extend equipment lifespan by 25% through regular inspections and adjustments.
- Decrease emergency interventions by 50%, cutting production losses and unexpected costs.
2.2. A Direct Impact on Productivity
By reducing failures and optimizing machine usage, first-level maintenance enhances industrial performance.
Companies that have implemented digitalized maintenance observe:
- +15% improvement in OEE (Overall Equipment Effectiveness), a key performance indicator.
- -45% reduction in micro-stoppages, which disrupt production flow.
- +20% increase in machine availability, ensuring a smoother workflow.
Discover how Veolia optimized its maintenance with Picomto and transformed its asset management!
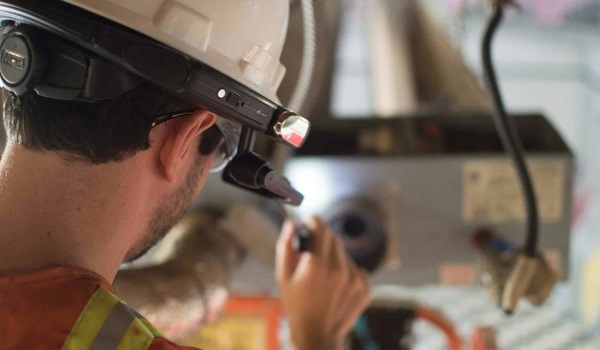
3. What Are the Typical First-Level Maintenance Operations?
First-level maintenance is based on simple yet crucial actions. When performed regularly, they help prevent 60% of common failures and ensure smooth equipment operation.
3.1. What Daily Actions Should Be Performed?
To be effective, first-level maintenance should be integrated into operators’ daily routines. The key actions include:
- Visual inspections: Detecting potential anomalies (wear, leaks, deterioration).
- Workstation cleaning: Removing dust and residues that could harm machines.
- Fluid level checks: Ensuring sufficient oil, lubricant, or coolant.
- Lubrication operations: Preventing premature wear of moving parts.
Performing these tasks regularly helps extend equipment lifespan and minimize production downtime.
3.2. How to Organize Effectively?
Good organization is the key to successful maintenance. To achieve this:
- Use a detailed checklist: Each operator knows exactly what tasks to perform.
- Implement a digital schedule: Ensures clear tracking and better intervention traceability.
- Leverage connected tools: Enables real-time reporting and optimized corrective actions.
With a structured approach, maintenance becomes a powerful driver of industrial performance!
4. How to Digitize First-Level Maintenance?
Digital transformation is revolutionizing industrial maintenance management.
By leveraging digital tools, intervention efficiency increases by 40%, significantly reducing unexpected downtime and boosting productivity.
4.1. The Benefits of Digitalization in Maintenance
Integrating digital solutions into first-level maintenance offers three major advantages:
- Standardized procedures: Operators follow clear, precise instructions.
- Real-time monitoring: All interventions are recorded, facilitating performance analysis.
- Fast and effective training: Teams upskill more quickly with interactive resources.
4.2. How Does Picomto Optimize Maintenance Management?
Picomto provides a comprehensive, user-friendly solution that allows you to:
- Create and digitize procedures to ensure execution aligns with standards.
- Monitor interventions in real time and centralize critical data.
- Train teams with interactive materials, reducing learning time.
Analyze performance and optimize processes with intelligent dashboards.
Conclusion
First-level maintenance is a fundamental pillar of industrial performance. By integrating simple and regular actions, it reduces breakdowns, optimizes costs, and improves equipment availability.
With digitalization, its impact becomes even more significant. Solutions like Picomto transform these processes by automating monitoring, simplifying training, and enhancing performance analysis.
The result? Faster, more efficient, and fully controlled maintenance. Take action today and boost your productivity with digitalization!
FAQ
Q: What is first-level maintenance?
A: It includes basic operations performed by operators: cleaning, lubrication, and daily visual inspections.
Q: What are the five levels of maintenance?
A:
- Level 1: Simple adjustments
- Level 2: Basic troubleshooting
- Level 3: Fault diagnosis
- Level 4: Major repairs
- Level 5: Overhaul/reconstruction
Q: What is level 3 maintenance?
A: It involves diagnosing and repairing complex faults by qualified technicians.
Q: What is the goal of maintenance?
A: To ensure equipment reliability, reduce operating costs, and extend lifespan.
Q: What are the four types of maintenance?
A: Preventive (planned), corrective (after failure), conditional (based on condition), and predictive (anticipatory).
Q: What is the difference between maintenance and servicing?
A: Servicing includes basic upkeep, while maintenance encompasses all preventive and corrective interventions.
Q: How to ensure effective maintenance?
A: Plan interventions, train teams, use digital tools, and track performance indicators.
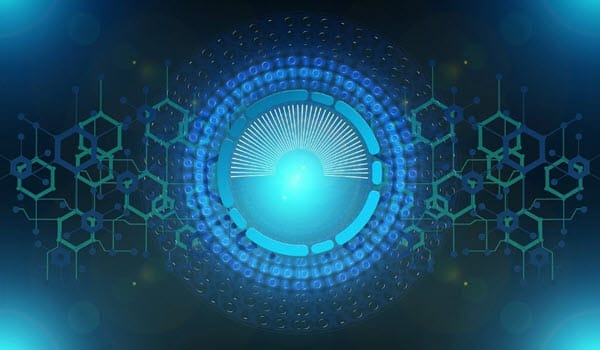
Leave A Comment