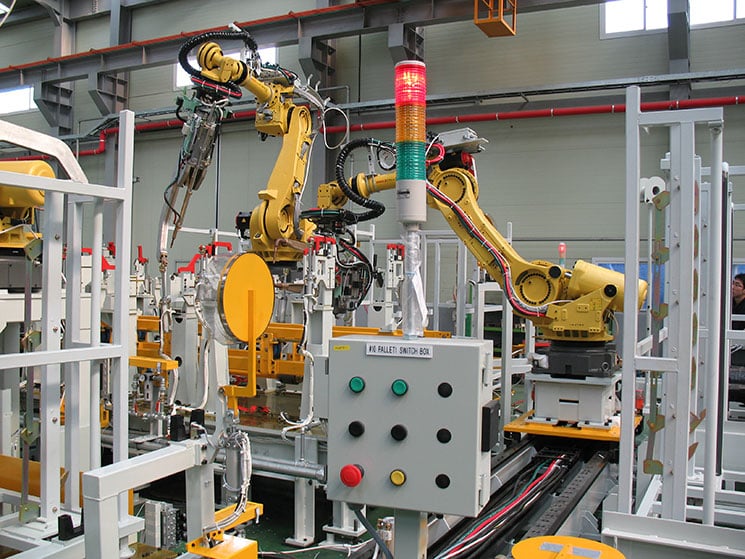
The industry of the future is already in motion. It is characterized in particular by the use of increasingly complex and sophisticated tools, those related to digital technology, and therefore requires the adaptation of the skills of technicians and engineers to these technologies.
In the context of the Smart Industry, this upskilling becomes essential to fully leverage connected systems, data-driven processes, and automation.
Training is, therefore, a crucial element in this relentless evolution.
Major changes in industrial activities
Industrial engineers and technicians are inevitably led to rethinking their skills with the arrival of new digital tools and robotization in industry. The changes brought about by these technological innovations have a direct impact not only on the nature of the positions and the skills associated with them but also on the organization of work within the industry.
The ever-increasing importance of 3D printing, automation, the Internet of Things, digital, connected production equipment and other technological innovations characterizing the industry of the future, imposes new requirements on the qualifications of the various plant actors, whether they are responsible for designing, supervising, supervising or executing production operations.
While these new tools hold great promise in terms of productivity, efficiency, flexibility, error reduction and customization of production, they lose all interest if they are not implemented or handled by people with all the necessary knowledge and know-how. Because whatever the levels of progress made in the field of technology for industry, the human factor remains central.
The major challenge for decision-makers and company managers is, therefore, to ensure that the evolution of their teams’ skills follows that of hardware and software resources.
Ensure adaptation to new tools and the transmission of know-how
For the skills of industrial engineers and technicians to be adapted to these new requirements, training is undeniably the key. Business leaders are well aware of this. Christophe Sirugue, Secretary of State for Industry quoted by Les Echos (December 2016) *, explains that “in the digital world, training is clearly the challenge of 2017″ and that “the business leaders[he meets] are now talking less about taxation than about recruitment and training. There is a consensus that this is the area where we absolutely must act. »
By being trained in the latest digital technologies, employees are called upon to integrate complementary knowledge with their own, such as those related to virtualization, simulation or data processing. At the same time, jobs such as “data scientist” are emerging and are particularly sought after, but they can only really be productive if they include a knowledge of the industrial process.
It is therefore up to manufacturers to implement the appropriate strategies: internal training sessions, continuous training plan, know-how transfer mechanisms, etc. An approach that presents difficulties (significant financial resources required, immobilization of personnel during their training, reorganization of services, etc.), but without which it is impossible to remain competitive.
About Picomto
Picomto is the web and mobile software solution for creating, managing, sharing, consulting and analyzing visual work instructions.
* Source: https://www.lesechos.fr/09/12/2016/LesEchos/22336-083-ECH_l-industrie-du-futur-bute-sur-la-formation-au-numerique.htm#JBerwUOpxK64qSp7.99
Leave A Comment