Wondering how to enhance your company’s performance? Quality management has become an indispensable strategic lever in today’s business landscape. In an increasingly competitive economic environment, mastering processes is crucial. At a time when 67% of companies consider quality a top priority, the digitalization of procedures has become a necessity.
Digital solutions are profoundly transforming how we manage quality. For instance, companies that digitize their procedures report a 45% reduction in non-conformities. Additionally, centralizing quality documents on a single platform saves significant time.
Whether you’re a beginner or a quality expert, this article will guide you step by step. Together, we’ll explore the fundamentals, methods, and essential tools to successfully implement your quality initiative.
Key Takeaways
Quality management improves customer satisfaction by 25% on average
⚡ 85% of ISO 9001-certified companies report increased productivity
Average operational cost reduction of 23% after implementation
Non-conformity rates drop by 48% after the first year
⭐ 92% of customers prefer quality-certified companies
67% of companies increase their market share after certification
1. What is Quality Management and Why is it Essential Today?
Quality management is much more than simply inspecting finished products. It encompasses all processes that ensure a company’s operational excellence.
According to a 2023 AFNOR study, 78% of companies now consider quality a key differentiator.
1.1. How to Define Quality Management in Business?
Quality management is a methodical approach to optimizing performance. It relies on four fundamental pillars: task planning, execution, control, and continuous improvement.
For example, Toyota revolutionized the automotive industry with its Kaizen method, reducing production defects by 98%.
1.2. What Are the Fundamental Principles to Know?
First and foremost, quality initiatives are customer-focused.
A McKinsey survey reveals that 70% of purchasing experiences depend on service quality. Additionally, employee involvement plays a crucial role. Moreover, a process-oriented approach clearly identifies individual responsibilities.
1.3. How Does Quality Management Differ from Quality Control?
Quality control is only one part of a quality management system. In reality, quality management goes further by integrating defect prevention. For example, companies adopting a preventive approach reduce their cost of poor quality by 40% on average.
2. What Are the Concrete Benefits of a Quality Management System?
Implementing a quality system generates measurable benefits.
According to a 2023 ISO study, 92% of certified companies report significant performance improvements.
2.1. How Does Quality Management Improve Customer Satisfaction?
Customer satisfaction increases significantly through better process control. Indeed, ISO 9001-certified companies report an average 25% boost in customer satisfaction.
Additionally, complaint rates typically drop by 30% after implementing a quality system.
2.2. What Impact Does It Have on Cost Reduction and Productivity?
A quality system significantly optimizes operational costs.
Companies reduce their cost of poor quality by 15-25% on average. Furthermore, productivity increases by 20% through process optimization.
2.3. What Are the Benefits for Team Motivation?
Employee engagement improves markedly with a structured quality initiative. In this regard, 76% of employees feel more involved after system implementation. Moreover, turnover decreases by an average of 18%.
2.4. How to Measure Return on Investment?
The ROI of a quality initiative becomes measurable through several key indicators. For example, companies report an average reduction of 40% in costs.
3. How to Implement an Effective Quality Management System?
Implementing a quality management system requires a structured approach.
To date, 67% of companies that fail in their initiatives lack methodology. Above all, a progressive and planned approach is essential.
3.1. What Steps Should You Take to Start Your Quality Project?
First, management commitment is the foundation of any successful quality project. This translates into allocating dedicated resources.
For example, high-performing companies dedicate 2-3% of their budget to quality.
3.2. How to Conduct a Relevant Initial Assessment?
An initial assessment identifies strengths and areas for improvement.
In this regard, a Deloitte study shows that 85% of successful quality projects begin with a comprehensive audit. Additionally, digital tools greatly facilitate this analysis phase.
3.3. How to Effectively Engage Employees?
Employee involvement is a key success factor. Companies that train 100% of their staff in quality report a 50% reduction in non-conformities. Moreover, digitizing procedures facilitates the adoption of best practices.
4. What Are the Essential Tools for Quality Management?
Today, digital tools are revolutionizing quality management. According to a Gartner study, 73% of companies plan to increase their investments in these solutions.
4.1. How to Choose the Right Performance Indicators?
Selecting appropriate KPIs determines the effectiveness of quality steering.
For example, compliance rates, cost of poor quality, and customer satisfaction are essential indicators. Real-time monitoring enables quick action on deviations.
4.2. How to Implement an Effective Documentation System?
A high-performing documentation system relies on three pillars: accessibility, updates, and traceability.
Digitizing procedures reduces time spent on document management by 65%. It also ensures access to the latest document versions.
4.3. Which Digital Solutions Should You Prioritize?
Tool selection depends on specific company needs. However, certain features are indispensable:
- Centralized document management
- Approval workflows
- Real-time indicator tracking
- Non-conformity management
5. How to Obtain and Maintain ISO 9001 Certification?
ISO 9001 certification is an international recognition of a quality system. Currently, over one million companies are certified worldwide.
5.1. What Are the Key Requirements of ISO 9001?
The ISO 9001:2015 standard is based on seven fundamental principles.
In practice, a process approach and continuous improvement are essential pillars. Additionally, risk management now plays a central role.
5.2. How to Effectively Prepare for Certification?
Certification preparation requires a methodical approach.
Indeed, 65% of companies underestimate the time needed. First, establish a realistic timeline. Furthermore, team training is crucial.
5.3. What Are the Steps in the Certification Audit?
The certification audit consists of several distinct phases. First, the initial audit assesses system compliance. Then, the certification audit deepens the analysis.
For example, an audit typically lasts 2-5 days, depending on company size.
6. What Are the Best Practices by Industry?
Quality requirements vary by sector. Indeed, each industry has its specificities. An ISO study reveals that 78% of companies adapt their quality systems to their sector.
6.1. How to Adapt Quality Initiatives to Manufacturing?
Manufacturing requires particular attention to process control. For example, the automotive industry applies the IATF 16949 standard.
Additionally, traceability plays a crucial role in industrial production.
6.2. What Are the Specifics for the Service Sector?
The service sector prioritizes customer satisfaction. In this regard, 82% of service companies focus their quality initiatives on customer experience. Moreover, continuous staff training becomes paramount.
6.3. How to Apply Quality in the Medical Sector?
The medical sector follows strict standards. Specifically, the ISO 13485 standard governs medical devices. Additionally, risk management is central in this sector.
7. How to Ensure Continuous Improvement of Your Quality System?
Continuous improvement drives performance. According to a Deloitte study, companies that rigorously apply it increase productivity by 20%.
7.1. Which Indicators Should You Track for Progress?
Choosing the right indicators determines steering effectiveness. In practice, track:
- Customer satisfaction rate (target > 90%)
- Cost of poor quality (< 2% of revenue)
- Process compliance rate (> 95%)
7.2. How to Implement Effective Process Reviews?
Process reviews identify improvement areas. A quarterly frequency is optimal. Additionally, digital tools facilitate action plan tracking.
Conclusion
Quality management is a profitable investment for any company. Indeed, the benefits far outweigh initial costs. Moreover, digitalization significantly simplifies the process.
To succeed in your quality project, adopt a progressive approach. Additionally, team involvement is crucial. Finally, remember that quality is a continuous journey toward excellence.
The digital transformation of quality is now essential. In this regard, solutions like Picomto simplify document management and process tracking.
FAQ
Q: How long does it take to implement a quality system?
A: Implementation typically takes 6-12 months for an SME.
Q: Where should I start with a quality initiative?
A: Begin with an initial assessment and secure management commitment.
Q: Do I need a dedicated quality manager?
A: Yes, for companies with over 50 employees. SMEs can have a part-time referent.
Q: Is ISO certification mandatory?
A: No, but it’s often necessary to meet client and market requirements.
Q: What’s the ROI of a quality initiative?
A: Companies reduce costs by 15-25% on average after two years.
Q: How to maintain ISO certification?
A: Through regular audits and documented continuous improvement.
Q: Can all quality processes be digitized?
A: Yes, modern solutions enable 100% digital quality process management.
Q: What’s the difference between quality and quality control?
A: Quality encompasses all processes, while quality control only verifies final compliance.
Q: Should all employees be trained?
A: Yes, every employee should understand their role in the quality system.
Q: How to choose quality software?
A: Prioritize a solution tailored to your sector with an intuitive interface.
Q: Does quality work for all businesses?
A: Yes, but the approach must adapt to company size and industry.
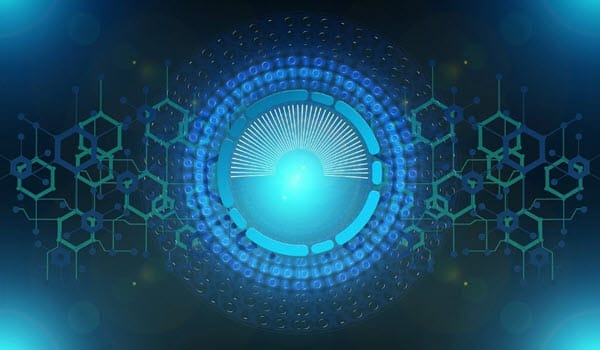
Leave A Comment