Did you know that scrap rate represents on average 3 to 8% of production in the manufacturing industry? This statistic reveals the magnitude of financial losses faced by industrial companies. Scrap rate corresponds to the percentage of defective or non-conforming products relative to total production. These losses directly impact profitability, reputation, and competitiveness of companies. The issues related to scrap rate go far beyond simple material losses. Indeed, they also encompass labor costs, compromised delivery schedules, and environmental impact. Consequently, mastering this rate becomes crucial for maintaining efficient and profitable production.
This article will guide you in understanding, calculating, and especially reducing your scrap rate through proven methods and innovative digital tools.
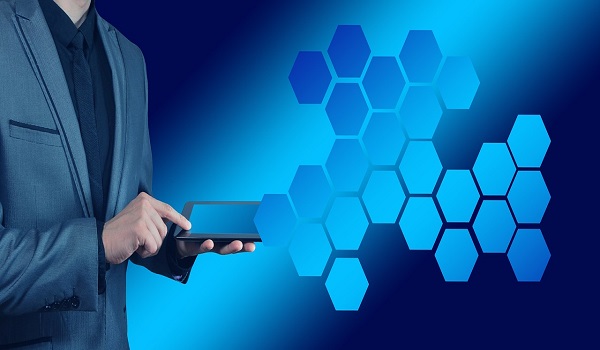
Key takeaways regarding scrap rate:
- Precise definition: Scrap rate measures the percentage of defective products relative to total production
- Major financial impact: Represents 3 to 8% average losses in the manufacturing industry
- Identifiable causes: Primarily linked to deficient procedures, training, and maintenance
- Standardized calculation: Simple formula but requiring precise and regular data
- Digital solutions: Significant reduction possible through process digitalization
Would you like a personalized analysis of your scrap rate?
Contact our experts for a free diagnostic of your production.
1. What is scrap rate and why is it crucial?
Scrap rate constitutes a fundamental key performance indicator (KPI) for any industrial company. It reveals the efficiency of your production processes and identifies improvement opportunities. Furthermore, its mastery directly influences your market competitiveness.
1.1. Detailed definition and importance for production
Scrap rate expresses the ratio between defective products and total production over a given period. It encompasses all products that do not conform to defined quality standards. This measure allows evaluation of your manufacturing process efficiency.
The importance of this rate lies in its ability to:
- Identify dysfunctions in your production chains
- Measure the impact of implemented improvements
- Compare performance between different production lines
- Establish continuous improvement objectives
1.2. Direct impact on company profitability
A high scrap rate generates considerable hidden costs. First, it implies a direct loss of raw materials and production time. Then, it requires additional resources to reprocess or eliminate defective products.
Indirect costs include:
- Delivery delays and contractual penalties
- Additional storage costs
- Impact on customer satisfaction
- Increased quality insurance premiums
1.3. Difference between scrap and other production losses
Scrap rate distinguishes itself from other industrial performance indicators. Unlike recoverable waste, scrap designates permanently lost products. It also differs from rework rate, which concerns repairable products.
This distinction enables more precise performance analysis and identification of specific improvement levers.
2. How to precisely calculate your scrap rate?
Calculating scrap rate requires a rigorous method and reliable data. A systematic approach guarantees the accuracy of your indicators and facilitates improvement tracking. Moreover, automating this calculation optimizes your time and reduces human errors.
2.1. The calculation formula explained step by step
The standard scrap rate formula is: (Quantity of defective products / Total quantity produced) × 100
This simple formula nevertheless requires clear definition of elements:
- Quantity of defective products: all products not conforming to specifications
- Total quantity produced: complete production over the analyzed period
- Reference period: generally daily, weekly, or monthly
2.2. Necessary data for reliable calculation
Precise scrap rate calculation requires quality data. First, you must systematically record all defective products. Second, complete traceability of your production proves indispensable.
Essential data includes:
- Quantities produced by workstation
- Nature and origin of observed defects
- Corresponding production time
- Operational conditions (team, equipment, raw materials)
2.3. Digital tools to automate monitoring
Modern digital solutions revolutionize scrap rate monitoring. Indeed, they enable automated data collection and real-time analysis. Thus, you obtain an instantaneous view of your performance.
Advantages of digital tools:
- Reduction of manual entry errors
- Automatic alerts when thresholds are exceeded
- Predictive analytics to anticipate problems
- Interactive and customizable dashboards
3. What are the main causes of high scrap rate?
Identifying root causes of high scrap rate constitutes the first step toward improvement. Generally, these causes group into three main categories: procedural, human, and technical. Nevertheless, their complex interaction requires in-depth analysis to determine action priorities.
3.1. Problems related to procedures and work instructions
Inadequate procedures often represent the main cause of high scrap rate. Obsolete, incomplete, or difficult-to-understand work instructions generate recurring errors. Consequently, standardization and regular updating of procedures become essential.
Typical procedural problems include:
- Ambiguous or contradictory instructions
- Procedures not adapted to technical evolutions
- Lack of modification traceability
- Absence of new procedure validation
3.2. Human factors and operator training
Human errors constitute a major source of waste in industrial production. Insufficient training, lack of experience, or fatigue directly influence quality. Moreover, the absence of quality awareness amplifies these problems.
Critical human factors include:
- Incomplete or inadequate initial training
- Lack of skill updates
- Work overload and operational stress
- Poor communication between teams
3.3. Technical failures and maintenance
Faulty equipment generates non-conforming products and increases scrap rate. Insufficient preventive maintenance or inappropriate adjustments compromise production quality. Furthermore, normal equipment wear requires rigorous monitoring.
Common technical failures:
- Tool and production equipment wear
- Frequent machine misalignments
- Corrective maintenance performed too late
- Absence of regular instrument calibration
4. How to effectively reduce your scrap rate?
Reducing scrap rate requires a methodical approach and adapted solutions. First, identifying root causes allows targeting priority actions. Then, implementing modern digital solutions accelerates improvements and ensures lasting results.
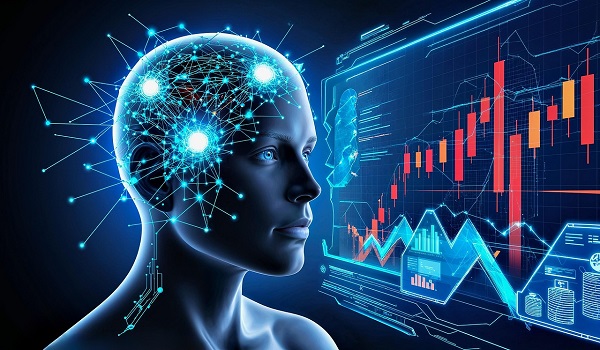
4.1. Procedure digitalization with Picomto
Digitalization of work instructions revolutionizes scrap rate reduction. Picomto offers a complete solution that guides operators step by step. This approach eliminates interpretation errors and guarantees procedure compliance.
Benefits of digitalization include:
- Visual and interactive instructions
- Real-time procedure updates
- Complete traceability of performed actions
- Immediate performance feedback
4.2. Team training and support
Team support constitutes an essential pillar of scrap rate reduction. Continuous and adapted training significantly improves operational performance. Furthermore, involving operators in continuous improvement strengthens their engagement.
Recommended training actions:
- Awareness of quality and cost issues
- Technical training on equipment
- Problem-solving skill development
- Individual and collective coaching
4.3. Continuous process analysis and optimization
Continuous process improvement guarantees sustainable scrap rate reduction. This approach relies on regular data analysis and identification of optimization opportunities. Consequently, it requires high-performance measurement and monitoring tools.
Steps of continuous optimization:
- Collection and analysis of production data
- Identification of bottlenecks
- Testing and validation of improvements
- Standardization of best practices
5. Which digital tools to master your scrap rate?
Digital tools radically transform scrap rate management in modern industry. They offer real-time visibility on performance and facilitate decision-making. Moreover, their integration with existing systems optimizes workflows and improves operational efficiency.
5.1. Advantages of modern digital solutions
Digital solutions bring considerable added value in scrap rate management. They enable automated data collection and advanced analytics. Thus, companies can anticipate problems rather than suffer their consequences.
Key advantages include:
- Real-time performance monitoring
- Predictive analytics for maintenance
- Automated reporting and alerts
- Integration with existing ERP systems
5.2. Presentation of the Picomto solution
Picomto offers a complete platform to reduce scrap rate through process digitalization. This solution guides operators with interactive instructions and automatically collects performance data. It adapts to all types of industries and easily integrates into existing environments.
Main Picomto functionalities:
- Digitalized and interactive work instructions
- Automatic quality data collection
- Customizable dashboards
- Integration with existing information systems
Conclusion
Scrap rate represents a major challenge for industrial competitiveness. Its mastery requires a comprehensive approach combining precise analysis, team training, and process digitalization. Modern solutions like Picomto offer considerable opportunities for loss reduction.
Digitalization of work instructions constitutes a powerful lever to improve quality and reduce costs. It enables practice standardization and complete operation traceability. Consequently, it significantly contributes to industrial performance optimization.
Investment in digital tools generates rapid return on investment through loss reduction and operational efficiency improvement.
FAQ
How to calculate scrap rate?
Formula: (Defective products / Total production) × 100
What is waste rate?
Percentage of non-conforming products relative to total production
How is waste rate calculated?
Same formula as scrap rate: defects divided by total production
How to calculate rejection rate?
Identical to scrap rate: rejections over total production times 100
How to perform rate calculation?
Divide the problematic quantity by total quantity, multiply by 100
What is wastage rate?
Synonym of scrap rate, measures definitive production losses
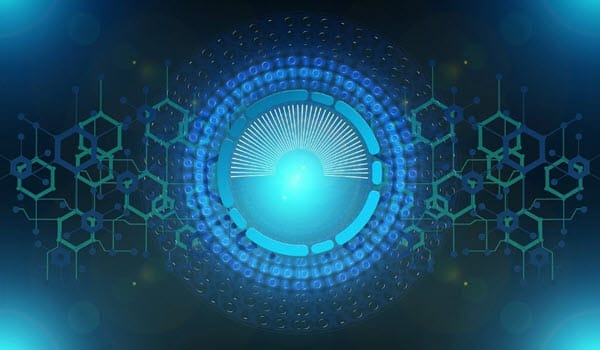
Leave A Comment