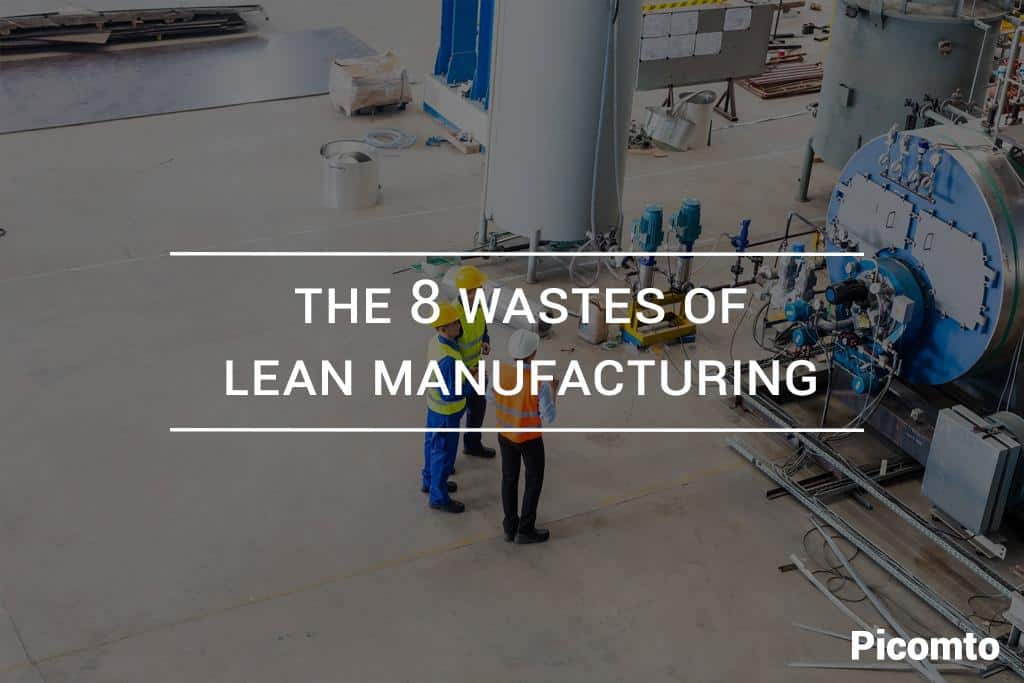
How to optimize its production and have a more efficient organization? Lean Manufacturing offers solutions that many companies have chosen to adopt and that have enabled them to achieve their objectives. The Kaizen method, combined with continuous improvement, relies heavily on the pursuit of wasteful sources, or muda, in order to achieve a more efficient production system.
In Lean Manufacturing, we first identified 7 major families of waste, then an 8th recently joined them:
- Overproduction
- Inventory
- The defects
- Extra Processing
- Waiting
- Transportation
- Motion
- Non-utilized Talent
1. Producing more than enough
Overproduction is the fear of any corporate manager. Creating more products than real demand is able to absorb, this generates considerable costs related to the accumulation of stocks and the heaviness affecting flows.
This is often a consequence of a production method based exclusively on sales forecasts.
Lean Manufacturing recommends aligning itself more with orders than with prospects that are at the mercy of market fluctuations.
2. Allow stocks to accumulate unnecessarily
Discussed earlier about overproduction, which is one of the main causes, the accumulation of unnecessary stocks is also very expensive for the company.
A “just-in-time” production method is promoted by Lean Manufacturing in order to minimize the quantities of work in progress and finished products, and thus reduce inventory congestion.
Otherwise, the organization may face significant losses in terms of space and resources.
3. Let the defects pass through
In Lean Manufacturing, we also strive to track down and prevent defects, as they have serious consequences. They require corrective operations that consume unnecessary resources and work time.
Moreover, if products with errors reach customers as they stand, the perception of the company and its brand by customers inevitably suffers.
4. Excessive steps
Any unnecessary step in a process increases production costs. An operation is considered disabling if its removal does not affect the conformity of the product with the customer’s expectations.
Within the framework of a Lean Manufacturing approach that relies on Kaizen continuous improvement, therefore, only those steps that have real added value will be considered
5. Having to manage waiting times
Waiting times, resulting from breakdowns, malfunctions, supply problems or, more generally, non-optimized flows, strongly penalize the company’s productivity.
Here again, Lean Manufacturing recommends reviewing all aspects that slow down manufacturing processes.
6. Embedding yourself in unnecessary movements
A handful of seconds lost during an operation due to unnecessary movements are transformed into minutes and then hours by adding them together as the operation is reproduced. That is so much time and energy wasted due to an ergonomically inadequate workstation, poorly organized tools or documents, inadequate procedures…
7. Make unnecessary trips
In order to save time, energy and resources, Lean Manufacturing requires that the movement of employees, parts and products be optimized.
There are various tools available for this purpose, including the spaghetti chart. It consists in drawing up a representation of physical flows in order to identify more easily the movements that can be shortened.
Digital solutions as part of smart manufacturing also make it possible to simulate these flows before and after making improvements in order to measure their effectiveness.
8. Not making the most of skills
Finally, the 8th and last waste apprehended by Lean Manufacturing is the insufficient use of the skills available to the company. Not taking full advantage of the know-how and business knowledge already in place penalizes the organization in various ways: loss of efficiency, unnecessary recruitment, demotivation of employees who are deprived of recognition.
Bonus : Not using an adequate solution
Picomto is the leading digital work instructions software allowing ccompanies to reduce human factors. Do not hesitate to contact us if you have any questions.
Leave A Comment