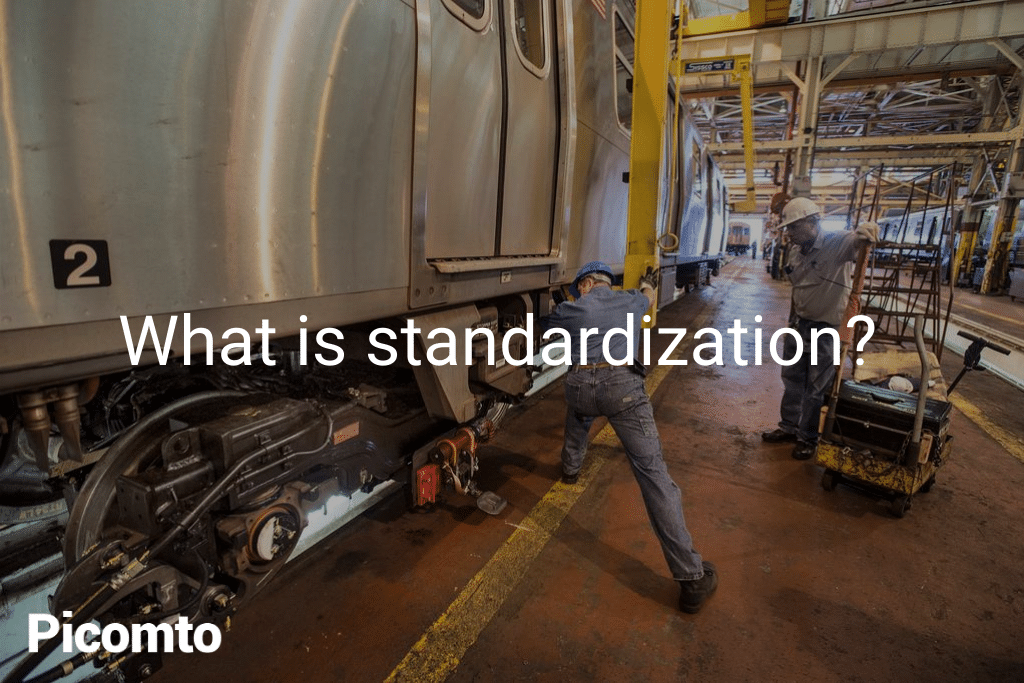
Standardization is one of the major actors in the success story of Japanese industry, and then in other countries that have had a good idea to follow in its footsteps.
- What are the principles?
- What improvements does it allow?
- What are the conditions for success?
Standardization: a listing of operations to standardize actions
Standardization began in the 1950s and 1960s in Japan, more specifically at Toyota. Two Japanese industrialists are considered as the fathers: Taiichi Ohno and Shigeo Shingo. This strategic choice was part of a logic of economic recovery and maximum efficiency led by the country of the Rising Sun after the disaster of the Second World War. And it has paid off by significantly helping the Japanese industry to become one of the most efficient in the world.
Toyota-style standardization has even become a model that is still being followed, studied and revisited today.
It consists in promoting the mass production of standard models by setting up reference standards. In a Lean Manufacturing approach, it is a question of listing and describing the operations to be carried out by each employee in each position. Standardization also involves identifying the means and resources to be used to achieve predefined results.
At the same time, it emphasizes specific aspects of industrial activity such as safety and quality actions.
The standards thus developed are documented, taking various forms: procedures, work instructions, control sheets, technical specifications, safety instructions, etc.
Digital work instruction software, such as Picomto, makes it possible to create these types of documents while respecting the industrial standards in question but to standardize each document in the same way.
What benefits can we expect from standardization?
Standardization aims to eliminate process variations, as they are sources of errors. However, these have a cost, because their correction consumes material, time and resources. In this way, standardization makes operations more efficient.
It also makes it possible to adapt production to changes in customer demand, quantitatively speaking.
Standardization also helps to strengthen morale and motivation within teams, which also see their skills consolidated. The training of new employees also benefits from this through the reference documents it involves producing.
It is a method that is associated with the continuous improvement process, particularly of the Kaizen type, since Kaizen continuous improvement involves regularly modifying standards so that they remain at the service of performance. Taiichi Ohno says, in this regard, that “where there is no standard, there is no continuous improvement.”
The prerequisites for a successful standardization strategy
Standardization can only be successful if the conditions for success are in place. These prerequisites are as follows:
- The availability, accessibility and readability of reference documents: their users (employees) must be able to easily access and understand them just as easily in order to carry out their tasks correctly, in accordance with standards. The information they contain must be brief and clear in order to limit interpretations and prevent errors.
- Standard documents also need to be “brought to life”: these referential are not fixed. They are called into question and improved, but these updates must not lead to the cohabitation of old (and therefore erroneous) supports with new ones (those “updated”). The digitization of industrial documents provides valuable assistance in this respect.
- Standardization is a method whose success depends largely on the involvement of all stakeholders: site managers, operators and control agents.
Standardization with dedicated software
The standardization of industrial documents is greatly facilitated by the use of a dedicated solution for this purpose. At Picomto, a European leader in digital work instruction software, we focus all our efforts on providing a solution to the business problems of manufacturers in accordance with the standards and regulations in force.
Leave A Comment