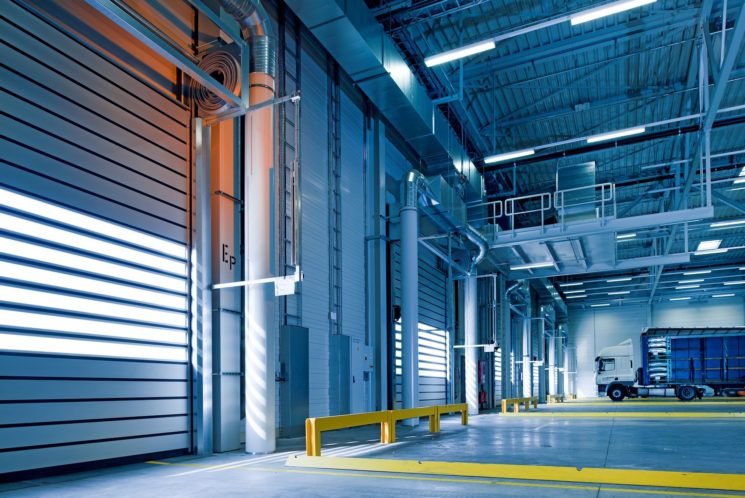
Developing and theorizing processes and methods is important in any industry. Nevertheless, these concepts, even if they are very precise and complete, are always confronted with the reality on the ground, which is inevitably made up of unexpected events, problems and various dysfunctions. This is why the managers are called upon to visit the production areas and workshops on a regular basis. This is what the Gemba Walk principle corresponds to, an activity that falls under Lean Management.
A better consideration of the reality on the ground
The Japanese word Gemba (or Genba) literally means “where reality is”, and therefore refers to a managerial activity consisting, for managers and decision-makers in the industry, in directly observing the processes at production equipment and operators.
The purpose of this approach is to identify, in person, possible sources of waste and dysfunctions that could hinder the company’s performance, but also to identify opportunities for improvement.
For the people in charge of this Gemba Walk, it is a question of closely studying the different stages of production, from raw materials to finished products ready to be delivered, as well as the physical and information flows. This proximity to the field allows information to be collected directly, so that it can be analyzed later, and changes can be made.
This “factory tour” must therefore be properly prepared, including the establishment of a list of predefined criteria that will serve as a basis for collecting information. It also implies a good prior knowledge of the processes, but it is also the one who will make the latter (knowledge of the processes) effective and more in line with the real situation.
This proximity to the ground allows several things:
- Evaluate more effectively the work done in workshops and production areas
- Ensure the proper application of lean processes, working methods and principles
- Identify the elements that create value and those that, on the contrary, generate waste and dysfunctions
To do this, the manager can proceed in two different ways: either by moving up the production flows from the finished product to the raw materials, or by moving in the opposite direction (from the raw materials to the shipment of the finished products). With the first approach, the manager puts himself, in a way, in the place of a customer who would like to know how his property is produced.
Employee involvement, a key element of the Gemba Walk
The Gemba Walk places great importance on the involvement of men and women in the field in identifying and solving problems. The method invites managers to contact operators who are in contact with the means of production directly to ask them questions, solicit their opinions and gather their suggestions for improvement. It is, in fact, people who are confronted on a daily basis with the reality on the ground who are best placed to report on problems relating to their specialties and propose solutions. Listening and interactivity are therefore essential qualities to be implemented during Gemba Walk’s work.
The analysis of the situation requires asking relevant questions, either established in advance during the preparation phase of the factory tour or imposed by field observations. The manager can, to take a concrete example, ask if the pile of pallets seen in the corridor does not hinder the movement of operators or handling machines. A detail which, like this one, may seem insignificant at first sight, is likely to improve production efficiency by making travel easier, in this case.
Once the information has been collected, it will then be necessary to carry out a precise analysis, implement the necessary corrective measures and ensure follow-up between the regular Gemba Walk sessions. This approach is part of a continuous improvement approach, with the aim of boosting performance and guaranteeing customer satisfaction.
About Picomto
Picomto is the web and mobile solution to create, manage, share, consult and analyze visual work instructions.
Leave A Comment