In an industrial context where every minute of downtime costs dearly, does the machine occupancy rate truly represent a key performance indicator? How can companies transform this KPI into a growth lever? Indeed, the machine occupancy rate constitutes a fundamental pillar of modern industrial optimization. This indicator measures the actual efficiency of your production equipment. Consequently, its optimization directly impacts your company’s profitability. Nevertheless, many organizations still struggle to fully exploit this potential. Thus, understanding and mastering this concept becomes essential to remain competitive in Industry 4.0.
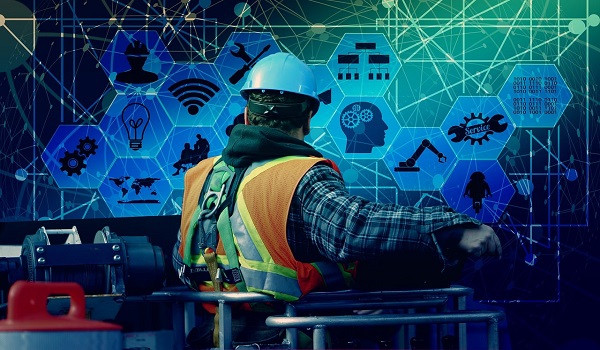
Key takeaways regarding machine occupancy rate:
- Precise definition: The occupancy rate measures the percentage of effective utilization time of a machine relative to available time
- Financial impact: A 10% improvement in occupancy rate can increase profitability by 15-20%
- Critical factors: The quality of work instructions, operator training, and preventive maintenance directly influence this KPI
- Digitalization: Digital solutions enable optimization of occupancy rates up to 25%
- Continuous measurement: Real-time monitoring proves essential for rapidly detecting deviations
Contact our experts for a personalized analysis of your current occupancy rate and discover solutions adapted to your industry sector.
1. What exactly is the machine occupancy rate?
The machine occupancy rate constitutes a fundamental indicator in modern industry. However, its precise understanding sometimes remains unclear for certain production managers.
Indeed, this metric goes well beyond a simple mathematical calculation. It truly reflects the operational efficiency of your industrial equipment.
1.1. Definition and importance in Industry 4.0
The machine occupancy rate represents the ratio between effective utilization time and total available time.
Concretely, it is expressed as a percentage and indicates the utilization efficiency of your equipment. In Industry 4.0, this indicator becomes crucial for:
- Optimizing equipment investments
- Reducing production costs
- Improving overall competitiveness
- Efficiently planning resources
1.2. Direct impact on production profitability
The economic impact of occupancy rate proves considerable. Indeed, an underutilized machine generates fixed costs without creating added value. Conversely, successful optimization allows to:
- Increase revenue without additional investment
- Reduce unit production costs
- Improve return on investment for equipment
- Free up capacity for new projects
1.3. Difference with other indicators (OEE, Overall Performance Rate)
The occupancy rate is clearly distinguished from OEE (Overall Equipment Effectiveness) and Overall Performance Rate.
While OEE integrates quality and performance, the occupancy rate focuses solely on temporal utilization. This simplified approach facilitates analysis and corrective action.
Discover our detailed case studies on occupancy rate optimization at Agromousquetaires to understand the real gains achieved.
2. How to effectively calculate your machine occupancy rate?
Mastering the calculation of machine occupancy rate constitutes the first step toward optimization. Nevertheless, beyond mathematical formulas, the measurement methodology determines result reliability.
Consequently, adopting a structured approach proves essential for obtaining actionable data.
2.1. The detailed calculation formula
The basic occupancy rate formula remains simple: Occupancy Rate = (Effective operating time / Available time) × 100
However, precise calculation requires considering:
- Effective operating time (actual production)
- Theoretical planning time
- Scheduled stops (maintenance, breaks)
- Unscheduled stops (breakdowns, adjustments)
2.2. Parameters to consider
To obtain a reliable calculation, several parameters must be integrated:
- Opening time: Planned operating hours
- Planned stops: Preventive maintenance, cleaning, shift changes
- Unplanned stops: Breakdowns, micro-stops, raw material waiting
- Cycle time: Theoretical duration for producing one piece
2.3. Available measurement tools
Several solutions allow precise measurement of this KPI:
- SCADA Systems: Automated equipment supervision
- IoT Sensors: Real-time data collection
- MES Software: Global production monitoring
- Mobile Solutions: Simplified field data entry
Participate in our webinar on training digitalization to discover modern measurement and optimization tools.
3. What are the factors that impact occupancy rate?
Optimizing machine occupancy rate depends on multiple interconnected factors. Indeed, identifying these improvement levers allows effective action on overall performance. Thus, a systemic approach is essential to maximize results.
3.1. Quality of work instructions
Clear and precise work instructions considerably reduce downtime. Indeed, poorly defined procedures generate:
- Handling errors
- Operational hesitations
- Work rework
- Frequent documentation consultations
3.2. Operator training
Operator competence directly influences machine efficiency. Appropriate training allows to:
- Reduce setup times
- Minimize production errors
- Optimize series changes
- Improve reactivity to incidents
3.3. Preventive maintenance
A well-planned maintenance strategy prevents unscheduled stops. Benefits include:
- Reduction of unexpected breakdowns
- Extension of equipment lifespan
- Optimization of maintenance costs
- Improvement of safety
3.4. Production planning
Optimized planning maximizes utilization of available capacities. Key elements include:
- Appropriate sequencing of manufacturing orders
- Intelligent management of series changes
- Synchronization of supplies
- Team coordination
Consult our Marine Nationale case study to discover how our solutions enabled optimization of their occupancy rate through better team training.
4. How to concretely improve your occupancy rate?
Improving machine occupancy rate requires a methodical and progressive approach. However, the most significant gains often come from digitalizing operational processes. Consequently, investing in the right technological solutions generates rapid return on investment.
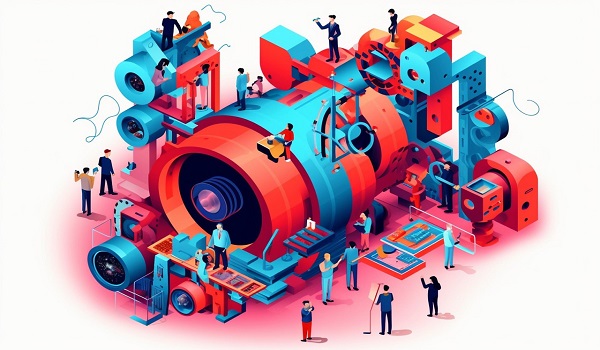
4.1. Digitalization of work procedures
Digital transformation of procedures revolutionizes operational efficiency. Benefits include:
- Instant access to instructions via tablets or smartphones
- Automatic procedure updates
- Step-by-step operator guidance
- Complete intervention traceability
4.2. Standardization of operating procedures
Uniformization of practices guarantees consistent performance. This approach allows to:
- Reduce variability in execution times
- Facilitate team versatility
- Improve production quality
- Simplify new employee training
4.3. Maintenance optimization
Intelligent maintenance maximizes equipment availability. Improvement areas include:
- Predictive maintenance based on data
- Optimized intervention planning
- Reduction of immobilization times
- Improvement of equipment reliability
4.4. Continuous team training
Investment in human skills proves profitable long-term. Benefits include:
- Improvement of individual productivity
- Reduction of operational errors
- Increased team autonomy
- Better adaptation to technological changes
5. Why digitize your work instructions with Picomto?
Digitalizing work instructions with Picomto radically transforms the approach to machine occupancy rates.
Indeed, our solution specifically addresses modern industrial challenges. Thus, companies adopting Picomto observe measurable improvements in their operational performance.
5.1. Measurable productivity gains
Picomto generates significant productivity gains through:
- Reduction of training times
- Decrease in procedural errors
- Optimization of intervention times
- Overall improvement of occupancy rate
5.2. Reduction of operational errors
Our solution minimizes human error risks through:
- Step-by-step visual guidance
- Automated compliance controls
- Real-time alerts
- Critical action validation
5.3. Better intervention traceability
Picomto ensures complete traceability via:
- Automatic intervention recording
- Precise action timestamping
- Individual performance tracking
- Detailed report generation
5.4. Remote technical support
Our solution facilitates technical assistance through:
- Integrated videoconferencing
- Real-time screen sharing
- Collaborative annotations
- Remote expertise
Discover our feedback from Veolia to understand the concrete impact of our solutions on occupancy rates.
Conclusion
Optimizing machine occupancy rates represents a major challenge for industrial competitiveness. Indeed, this indicator synthesizes operational efficiency and directly impacts profitability. Consequently, a structured approach combining precise measurement, analysis of influence factors, and process digitalization proves essential.
Digitalizing work instructions with Picomto offers a concrete and proven solution. Thus, our clients observe average improvements of 25% in their occupancy rate. Nevertheless, each industrial context remains unique and requires a personalized approach.
Request a personalized Picomto demonstration to discover how to concretely optimize your occupancy rate and transform your industrial performance.
FAQ
How to calculate occupancy rate?
Use the formula: (Effective time / Available time) × 100.
What is machine OEE?
OEE integrates availability, performance, and quality into a global indicator.
What is occupancy rate?
It’s the percentage of effective machine utilization over available time.
What’s the difference between OEE and Overall Performance Rate?
Overall Performance Rate includes pace losses.
What is the OEE formula?
OEE = Availability × Performance × Quality (expressed as percentage).
What is a good OEE?
An OEE above 85% is considered excellent in industry.
What is an acceptable scrap rate?
Generally less than 1% for optimal quality production.
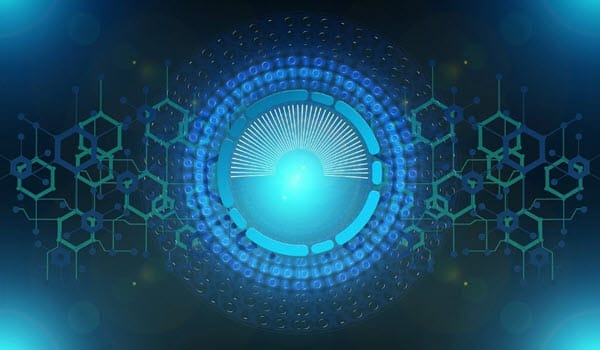
Leave A Comment