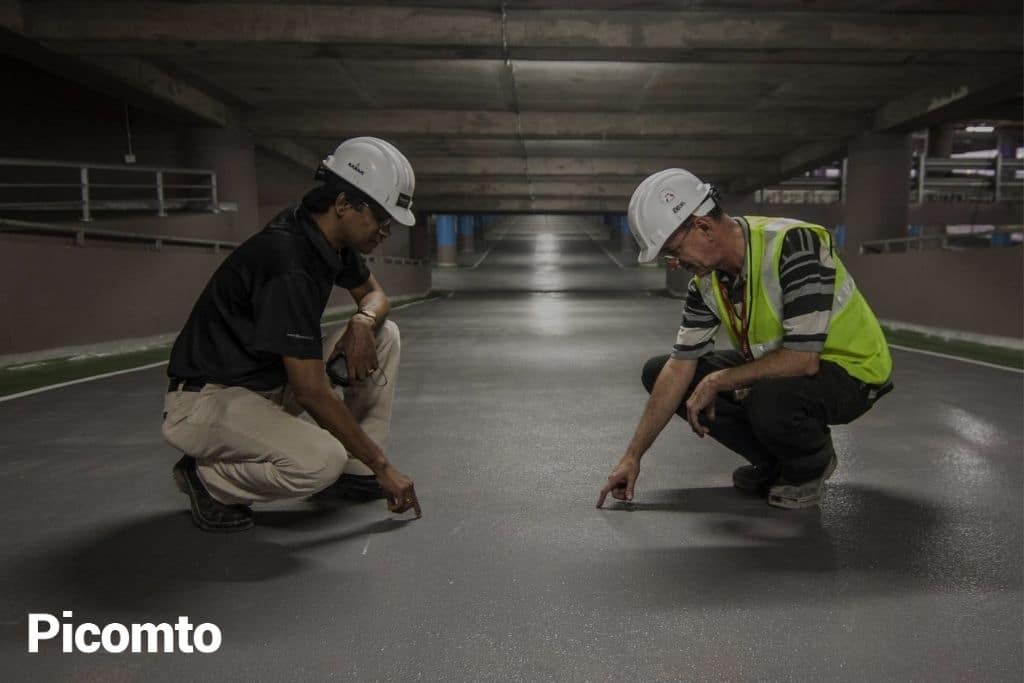
Each company essentially seeks to improve its performance, ensure high quality and improve productivity. To do this, the Lean management method is often used. It is a set of strategies to reduce or eliminate waste, then optimize quality and increase productivity.
Lean management: the main lines
Lean management principles are an interpretation of the production system that Toyota, a Japanese company, has known since the 1950s:
- Genchi genbutsu: find the source of the problem and solve it
- Kaizen: it is a continuous improvement process consisting of making a constant effort to involve superiors and employees to improve productivity and ensure operational excellence without investments.
- Challenge: without a challenge, there would be no innovative ideas. Without them, there would be no success.
- Respect: Larger companies owe their success to their employees. For this reason, they must be respected by providing good working conditions.
- Teamwork: Initiating the spirit of teamwork is important to ensure the success of a company.
Lean management: a philosophy in its own right
In addition to being a set of techniques that focus on Lean management, Lean management is a way of acting and thinking. It is a philosophy in its own right that can be applied to all types of industries, services and companies.
The philosophy of Lean management consists in ensuring performance management by optimizing productivity, quality, time and costs. The main goal is to satisfy the customer and stabilize operations. To achieve this, it is recommended to work on these 3 points of the company:
- The operational system: the main functions of the company that create added value for the customer.
- The management system: it is the set of activities through which the organization controls and implements its strategies and its operational system.
- Corporate culture: Imposing a corporate culture within your organization means giving it a strong identity and, above all, common values from which all members of the organization draw. This ensures lasting change.
Why does it work?
“Thanks to lean management, employees have the chance to work differently and with less stress“. Hubert Siegfriedt, Director of Leadership Consulting, rightly states: “From the Japanese, we learned rigour, discipline and logical organization while taking time. Forced labour has never been a good thing.” “Lean is among other things a tool against offshoring by reducing costs.”
It remains to be noted that large companies such as Renault and PSA Peugeot Citroën are implementing this management strategy, which confirms its effectiveness.
As each medal has its counterpart, lead management has its limits. Or more precisely, the approach can be counterproductive if its principles are not properly applied. For example, psychosocial and musculoskeletal disorders can develop in a team overstretched by trying to minimize waiting times.
With Picomto, your work instructions and SOP are part of a continuous improvement process. Create, use and analyze work instructions in a visual and interactive way. Feel free to contact us for more information.
Leave A Comment