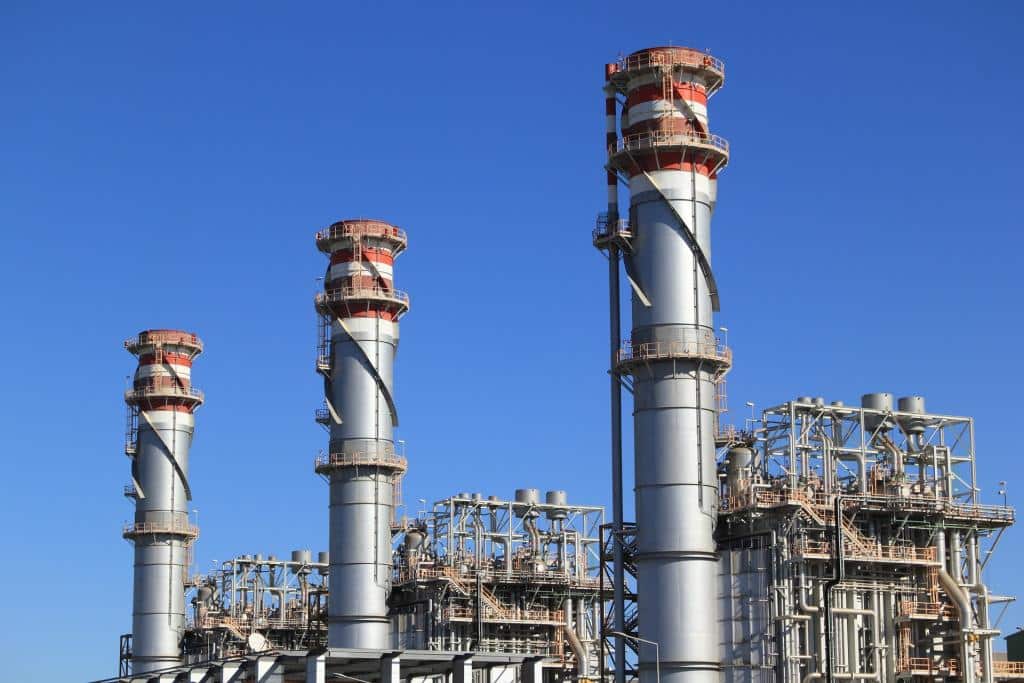
In many sectors and for discerning customers, ISO 9001 certification is a guarantee of quality and therefore satisfaction. In other words, it is a criterion on which they can base their selection between companies. This management standard is therefore an undeniable asset for any organization seeking to develop and gain market share in an increasingly competitive environment. As part of the industries’ strategy, it aims to help them become more efficient and better able to meet or exceed customer expectations. It is, without a doubt, one of the key elements of the 4.0 industry.
Stick to QMS requirements
When you think of quality, QMS (quality management system) and continuous improvement, you have to think of ISO 9001. It is, in fact, the fundamental support for companies aiming to strengthen their presence in the markets by focusing on an approach of efficiency and optimization.
The main objective of establishing this standard is to support companies towards a long-term approach based on the principle of continuous improvement. It defines QMS requirements and focuses on customer satisfaction.
In its 2015 version, it is marked by important changes, encouraging, in particular, to re-examine the quality approach to make it better adapted to the strategy of the industries, but also to better integrate risks and opportunities.
While the ISO 9001 standard encourages the consideration of customer expectations, it also promotes the integration of the needs of employees and partners (suppliers) into the company’s policy.
The principles of the ISO 9001 standard in its 2015 version and their application in the industry
The application of the ISO 9001 standard for industries requires compliance with 7 fundamental principles, which facilitate the implementation of the quality management system.
- Customer orientation: for organizations, this means ensuring that current and future customer needs are met by deploying the tools and techniques to do so.
- Leadership: The ability to lead and ensure that everyone in the organization knows their role and the objectives to be achieved.
- Involvement of staff: it is not enough to have competent staff. They must also feel involved to create value.
- Process approach: ISO 9001 considers that only an organization in which activities are considered as interdependent processes can aspire to efficiency gains.
- Improvement: the assumption here is that every aspect of industry activity can be improved in one way or another. Hence the need to constantly search for the points to be optimized and the tools to do so.
- Evidence-based decision-making: Evaluating and analyzing information is the key to maximizing your chances of achieving your goals.
- Stakeholder relationship management: the quality of relationships with suppliers and partners in general supports sustainable performance.
ISO 9001: what are the benefits for the company?
By integrating ISO 9001 into their strategy, industries gain better control of their internal operations while strengthening the confidence of customers and suppliers.
This approach makes it possible to define your objectives with greater precision and to aspire to new business opportunities through a realistic assessment of the environment and the context in which you operate. At the same time, it promotes efficiency and productivity through the process approach and its understanding by all employees.
It is a lever for customer loyalty and attraction by satisfying their needs through quality.
Finally, the ISO 9001 standard requires the company to identify and manage the risks associated with its activity.
Digital Work Instructions & ISO 9001
Digital work instructions softwares make easier to be compliant with the ISO 9001 standard, with automatic workflow, version control etc.. You want to know more about it ? Request a demo of Picomto !
Leave A Comment