Combien coûte une heure d’arrêt de production dans votre usine ? 10 000 € ? 50 000 € ? La maintenance préventive devient aujourd’hui indispensable pour éviter ces pertes. En effet, les pannes imprévues impactent directement votre rentabilité. Selon une étude récente de l’AFNOR, une stratégie de maintenance préventive efficace réduit les temps d’arrêt de 45% en moyenne.
Points clés à retenir concernant la maintenance préventive :
- La maintenance préventive réduit jusqu’à 60% les pannes imprévues
- Elle augmente la durée de vie des équipements de 25-30%
- Elle permet d’économiser 12-18% sur les coûts de maintenance
- Elle améliore la productivité globale de 20% en moyenne
- Elle diminue les risques d’accidents de 70%
1. Qu’est-ce que la maintenance préventive et pourquoi est-elle indispensable ?
La maintenance préventive regroupe l’ensemble des opérations planifiées qui visent à éviter l’apparition de pannes sur les équipements industriels.
Contrairement à la maintenance corrective, elle n’attend pas qu’une défaillance survienne. Elle anticipe. Elle repose sur l’analyse du fonctionnement des machines et intervient avant tout dysfonctionnement.
Son objectif est simple mais stratégique : maintenir un haut niveau de performance tout en limitant les interruptions. Elle s’inscrit ainsi dans une logique de fiabilité, de productivité et de maîtrise des coûts.
Cette approche devient essentielle dans un contexte industriel où les arrêts imprévus coûtent cher et désorganisent l’ensemble de la chaîne de production.
1.1. Comment fonctionne la maintenance préventive ?
La mise en œuvre de la maintenance préventive repose sur un protocole rigoureux. Elle s’appuie sur un calendrier d’interventions, établi selon les recommandations des constructeurs ou les retours d’expérience terrain.
Les techniciens effectuent des vérifications planifiées, selon des procédures standardisées. Chaque point de contrôle est documenté, chaque relevé analysé. L’objectif est d’identifier les premiers signes d’usure ou de dérive.
Cette approche proactive repose également sur la collecte de données. Elle permet de prendre des décisions éclairées, basées sur des faits et non sur des urgences.
Une étude menée par Veolia a démontré les effets concrets de cette méthode. Grâce à une maintenance préventive bien orchestrée, les entreprises peuvent :
- Réduire leurs coûts globaux de maintenance de 18 %
- Amortir l’investissement initial en moins d’un an
1.2. Quels sont les avantages concrets de la maintenance préventive ?
Les bénéfices de la maintenance préventive sont multiples et tangibles. Elle transforme la manière dont les entreprises gèrent leurs équipements.
Voici les résultats constatés dans de nombreux environnements industriels :
- Une réduction des arrêts de production non planifiés de 45 %
- Une augmentation de la durée de vie des équipements de 25 %
- Une diminution des coûts liés aux pièces détachées de 20 %
- Une amélioration de la sécurité, avec 70 % d’accidents en moins
Au-delà des chiffres, c’est toute la culture de la performance qui s’améliore. Les équipes gagnent en sérénité. Les responsables techniques prennent le contrôle de leurs opérations. Et les entreprises avancent avec un parc machines mieux maîtrisé.
2. Quels sont les différents types de maintenance préventive à votre disposition ?
Mettre en place une stratégie de maintenance efficace suppose d’en connaître toutes les composantes. En effet, la maintenance préventive ne se limite pas à une seule méthode. Elle regroupe plusieurs approches complémentaires, chacune adaptée à des contextes industriels spécifiques.
Avant d’agir, il est donc essentiel de bien choisir la méthode correspondant à vos enjeux de production, vos contraintes techniques et vos ressources disponibles.
Découvrez comment Daher a optimisé sa maintenance grâce à la digitalisation !
2.1. La maintenance systématique : une approche planifiée
Cette méthode repose sur un calendrier d’interventions défini à l’avance. Les actions de maintenance sont déclenchées selon une fréquence régulière, indépendamment de l’état réel de l’équipement.
C’est une approche simple, idéale pour les équipements à cycle de vie connu ou soumis à des réglementations strictes.
Concrètement, cela peut inclure :
- Le remplacement d’un filtre toutes les 500 heures de fonctionnement
- Le graissage systématique d’un roulement chaque semaine
- La vidange d’un moteur tous les trois mois
Cette méthode présente l’avantage d’être facile à mettre en œuvre. Elle permet aussi de mieux organiser les ressources humaines et matérielles.
2.2. La maintenance conditionnelle : une surveillance en temps réel
Cette méthode repose sur l’observation directe de l’état de l’équipement. Des capteurs mesurent en continu des paramètres comme les vibrations, la température ou la pression. Les interventions sont déclenchées uniquement si une dérive est détectée.
Elle est particulièrement adaptée aux machines critiques, où chaque arrêt non planifié entraîne des pertes importantes.
Parmi les actions fréquentes, on trouve :
- L’analyse vibratoire pour détecter les jeux anormaux
- Le suivi thermique pour repérer une surchauffe
- La mesure d’épaisseur pour anticiper l’usure
Cette surveillance en temps réel permet d’agir uniquement quand c’est nécessaire, tout en évitant les interventions inutiles.
Un exemple inspirant :
Grâce à la maintenance conditionnelle, Veolia a réduit ses coûts de maintenance de 25 %. L’entreprise anticipe désormais plus de 80 % des défaillances, évitant ainsi des interruptions coûteuses.
3. Comment mettre en place un plan de maintenance préventive efficace ?
Réussir l’implémentation d’un plan de maintenance préventive ne s’improvise pas. Cela demande une approche structurée, des outils adaptés et une implication transversale. Les entreprises les plus performantes suivent un processus clair, étape par étape.
L’objectif est de passer d’une logique de réaction à une logique d’anticipation. Pour cela, chaque action doit être pensée, documentée et suivie dans le temps.
Participez à notre webinar « Instructions de travail digitalisées »
3.1. L’évaluation initiale : une étape cruciale
Avant toute chose, il est indispensable de faire un état des lieux complet. L’audit initial permet d’avoir une vision claire du parc machines. Il s’agit d’identifier les équipements les plus sensibles, ceux dont la défaillance aurait le plus d’impact sur la production.
L’analyse de criticité vient ensuite. Elle classe les machines selon leur importance stratégique, leur fréquence d’utilisation et leur historique de pannes. Ce travail de priorisation est essentiel pour affecter les ressources de manière optimale.
Voici les actions à engager dans cette première phase :
- Réaliser un inventaire détaillé des équipements
- Identifier les postes critiques pour la chaîne de production
- Classer les machines selon leur niveau de criticité
- Recueillir les historiques de pannes et d’interventions
Un retour d’expérience marquant :
La Marine Nationale a réduit ses temps d’arrêt de 50 % après avoir structuré cette phase. Leur équipe de maintenance utilise désormais ses ressources de manière ciblée, avec des résultats concrets.
3.2. La digitalisation : un accélérateur de performance
Le digital transforme la gestion de la maintenance. Aujourd’hui, les solutions numériques remplacent les formulaires papier, fiabilisent les données et simplifient les processus. Les techniciens gagnent un temps précieux sur le terrain.
Avec des outils comme Picomto, les procédures deviennent interactives. Chaque opérateur dispose des bonnes instructions, au bon moment. L’accès à l’information est immédiat, même en mobilité.
Voici quelques apports concrets de la digitalisation :
- Centralisation des procédures et des documents techniques
- Accès mobile aux plans de maintenance
- Suivi en temps réel des interventions
- Réduction des erreurs humaines
4. Comment optimiser votre maintenance préventive avec le digital ?
L’industrie entre dans une nouvelle ère. L’essor de l’industrie 4.0 transforme profondément les pratiques de maintenance. Grâce aux outils digitaux, il est désormais possible de structurer, fiabiliser et accélérer chaque intervention.
La digitalisation ne se limite pas à l’automatisation. Elle permet une meilleure anticipation, une gestion simplifiée des ressources et un suivi en temps réel des opérations.
4.1. Les outils essentiels de la maintenance moderne
Pour tirer pleinement parti du digital, certaines solutions deviennent incontournables. Elles permettent de centraliser les informations, de piloter les activités à distance et d’améliorer la collaboration entre les équipes.
Voici les principaux leviers technologiques à intégrer dans votre stratégie :
- La GMAO (Gestion de Maintenance Assistée par Ordinateur) centralise les plannings, les historiques et les rapports d’intervention. Elle offre une vision globale des équipements et de leur état.
- Les applications mobiles facilitent le travail des techniciens sur le terrain. Ils accèdent aux instructions en quelques clics, même en situation de mobilité.
- Les capteurs connectés détectent les anomalies en temps réel. Ils permettent d’automatiser la surveillance et de déclencher des actions dès qu’un seuil critique est atteint.
Selon une étude de l’AFNOR, la digitalisation permet de réduire les temps d’intervention de 35 %. Les équipes deviennent plus autonomes, mieux coordonnées et nettement plus efficaces.
4.2. Picomto : la solution pour une maintenance connectée
Parmi les solutions disponibles, Picomto se distingue par son approche orientée terrain. Cette application transforme les procédures papier en instructions digitales claires, interactives et accessibles à tout moment.
Elle répond aux besoins concrets des techniciens :
- Les modes opératoires sont digitalisés, illustrés et actualisés en temps réel
- L’application mobile guide les équipes pas à pas pendant leurs interventions
- Les retours terrain sont automatiquement enregistrés, facilitant le suivi qualité
Grâce à cette solution, les entreprises standardisent leurs pratiques tout en réduisant les erreurs humaines.
5. Comment mesurer l’efficacité de votre maintenance préventive ?
Une maintenance préventive bien pensée ne suffit pas. Pour qu’elle soit vraiment performante, il faut la mesurer. Le suivi régulier de données fiables permet de valider les actions en place, d’identifier les points faibles et de les corriger.
Cette démarche analytique repose sur des indicateurs clés. Elle transforme la maintenance en levier de performance globale, et non plus en simple fonction support.
5.1. Les KPIs essentiels à surveiller
Les indicateurs de performance, ou KPIs, offrent une lecture objective de l’efficacité de vos actions. Ils permettent de piloter votre stratégie avec précision, en se basant sur des données concrètes plutôt que sur des impressions.
Voici les indicateurs les plus pertinents à suivre dans le cadre d’une maintenance préventive :
- Le taux de disponibilité des équipements
Il mesure le temps pendant lequel une machine est opérationnelle. Plus ce taux est élevé, plus vos installations sont fiables. - Le MTBF (Mean Time Between Failures)
Ce temps moyen entre deux pannes indique la robustesse de vos équipements. Il doit augmenter au fil du temps si la stratégie est efficace. - Le ratio préventif/correctif
Il reflète l’équilibre de votre maintenance. Un bon indicateur montre une majorité d’interventions préventives. - Le taux de pannes
L’objectif est de le réduire de 50 % grâce à une meilleure anticipation. - Les coûts de maintenance
Ils doivent baisser de 15 à 20 % en optimisant les interventions et en limitant les réparations imprévues. - Le temps d’intervention
Il peut être réduit de 30 % avec de meilleures procédures et des outils digitaux. - La disponibilité des équipements
Elle peut s’améliorer de 25 % grâce à une planification optimisée.
5.2. L’amélioration continue : un processus essentiel
Suivre les bons indicateurs ne suffit pas. Encore faut-il les utiliser pour faire évoluer votre plan de maintenance. L’analyse régulière des résultats permet de détecter ce qui fonctionne et ce qui doit être ajusté.
Les retours d’expérience des techniciens jouent un rôle central. En partageant leurs observations, ils contribuent à l’enrichissement des procédures. Cette boucle d’amélioration continue crée une dynamique positive, au service de la performance globale.
Voici comment inscrire cette démarche dans le quotidien :
- Organiser des points de revue réguliers avec les équipes terrain
- Réviser les plans d’intervention en fonction des résultats observés
- Mettre à jour les instructions dès qu’un retour ou un incident le justifie
- Valoriser les suggestions d’amélioration remontées par les techniciens
Un exemple concret :
Chez AgroMousquetaires, cette approche a permis d’augmenter la productivité de 35 %. L’équipe maintenance ajuste ses pratiques en continu, avec des résultats visibles sur toute la chaîne de production.
Conclusion : Passez à l’action avec Picomto
La maintenance préventive représente aujourd’hui un levier majeur de performance industrielle. Sa digitalisation avec Picomto multiplie son efficacité par 3.
Nos clients constatent en moyenne :
- Moins de pannes en
- Des’économies sur la maintenance
- Plus de productivité
- ROI garanti
Contactez nos experts pour un audit personnalisé ! CTA Contact !
FAQ – Les questions essentielles sur la maintenance préventive
Q : Quelle est la différence entre maintenance préventive et corrective ?
R : La maintenance préventive anticipe les pannes, tandis que la corrective intervient après une défaillance.
Q : Par où commencer la maintenance préventive ?
R : Identifiez vos équipements critiques et créez un planning d’interventions régulières basé sur leur criticité.
Q : Quel est le retour sur investissement ?
R : Les entreprises constatent généralement un ROI en 6-12 mois avec 15-20% d’économies.
Q : Comment choisir entre maintenance systématique et conditionnelle ?
R : La systématique convient aux interventions régulières, la conditionnelle aux équipements avec capteurs.
Q : Comment digitaliser efficacement la maintenance ?
R : Commencez par digitaliser vos procédures avec Picomto, puis intégrez progressivement d’autres outils digitaux.
Q : Quels sont les KPIs prioritaires ?
R : Surveillez le taux de pannes, les coûts, les temps d’intervention et la disponibilité.
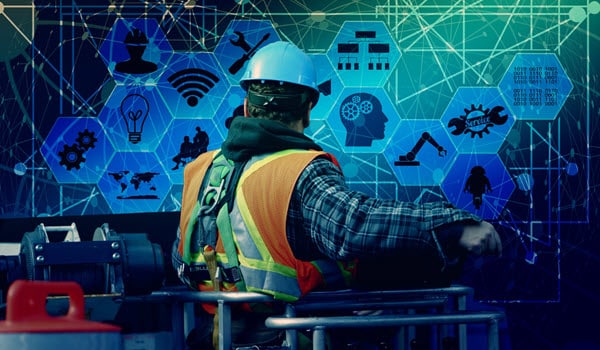
Laisser un commentaire