How did an automotive company reduce its production times by 30% in just 6 months? This spectacular transformation perfectly illustrates the crucial importance of production time optimization in modern industry. Production time refers to the total duration required to manufacture a product, from the beginning of the process to its completion. Indeed, this metric directly impacts profitability, competitiveness, and customer satisfaction. Consequently, mastering and optimizing these times becomes a major strategic challenge for any manufacturing company wishing to thrive in 2025.
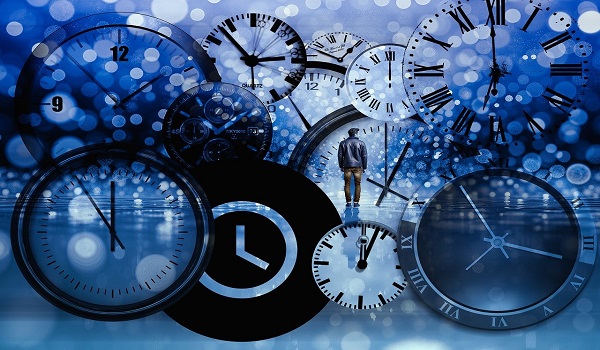
Key takeaways regarding production time:
- Definition: Production time encompasses all delays necessary for manufacturing a product
- Calculation: Total time = Setup time + Execution time + Control time
- Optimization: Lean methods and digitalization enable gains of 20-40%
- Measurement: Essential KPIs include OEE, cycle time, and downtime
- Stakes: Optimization directly impacts profitability and competitiveness
Do you want to transform your production process?
Contact our experts for a personalized analysis of your production times.
1. What exactly is production time?
Production time constitutes the backbone of any manufacturing process. Furthermore, this complex notion requires thorough understanding to be optimized effectively. Thus, we will explore its essential components and its impact on overall performance.
1.1. Detailed definition and key components
Production time represents the total duration required to transform raw materials into finished products. However, this definition encompasses several distinct components:
- Setup time: Machine configuration and workstation preparation
- Execution time: Transformation operations proper
- Control time: Quality checks and compliance verification
- Handling time: Movements and intermediate storage
- Waiting time: Inactive periods between stages
1.2. The different types of time to consider
Production time analysis reveals three main categories:
Value-added time:
- Operations adding value to the product
- Direct material transformations
Necessary time:
- Mandatory quality controls
- Technical adjustments and settings
Waste time:
- Unjustified waiting periods
- Unnecessary movements
- Breakdowns and malfunctions
1.3. Impact on overall company performance
Production times directly influence several key indicators:
- Profitability: 15-25% cost reduction possible
- Delivery times: Improved customer satisfaction
- Flexibility: Adaptation capacity to demand variations
- Competitiveness: Competitive advantage in the market
2. How to precisely calculate your production time?
Precise measurement of production times constitutes the foundation of any optimization approach. Indeed, without reliable data, it’s impossible to identify improvement areas. Nevertheless, this measurement requires rigorous methodology and adapted tools.
2.1. The calculation formula explained step by step
The basic formula revolves around three main components:
Production time = Setup time + Execution time + Finalization time
Calculation details:
- Setup time: Adjustments + Supply + Preliminary controls
- Execution time: Transformation operations × Quantity produced
- Finalization time: Controls + Packaging + Cleaning
Concrete example:
- Setup: 30 minutes
- Execution: 5 minutes × 100 pieces = 500 minutes
- Finalization: 20 minutes
- Total: 550 minutes or 9h10
2.2. Essential measurement tools
Modern technologies offer precise measurement solutions:
Traditional time study:
- Direct observation of operations
- Use of industrial stopwatches
- Structured recording sheets
Digital solutions:
- IoT sensors on machines
- Real-time tracking software
- Interactive dashboards
2.3. Common errors to avoid
Several pitfalls can distort measurements:
- Observation period too short: Lack of representativeness
- Neglecting downtime: Underestimation of actual durations
- Absence of standardization: Impossible comparisons between operators
- Forgetting changeover times: Impact on short runs
3. What are the factors influencing production time?
Understanding variables impacting production times allows identifying priority optimization levers. However, these factors interact with each other in complex ways. Thus, a systemic approach proves essential for sustainable improvement.
3.1. Human factors (skills, training…)
The human element remains central in production processes:
Technical skills:
- Mastery of craft gestures
- Equipment knowledge
- Problem-solving capability
Training and experience:
- Learning curve for new operators
- Continuous training on new technologies
- Experience sharing between teams
Motivation and engagement:
- Optimal working conditions
- Performance recognition
- Participation in improvements
3.2. Technical factors (equipment, maintenance…)
Technical infrastructure directly influences productivity:
Equipment condition:
- Age and wear of machines
- Preventive maintenance level
- Spare parts availability
Technologies used:
- Process automation
- Decision support tools
- Quality control systems
3.3. Work organization and procedures
Organizational structure significantly impacts performance:
- Production flow: Circuit optimization
- Standardization: Unified procedures
- Communication: Team coordination
- Planning: Efficient scheduling
4. How to concretely optimize your production times?
Production time optimization relies on proven methods and innovative technologies. However, success depends on a methodical and progressive approach. Consequently, we will present the most effective strategies to transform your processes.
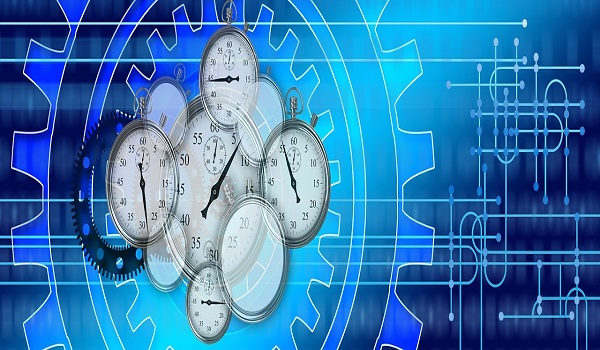
4.1. Proven methods (Lean, 5S…)
Lean Manufacturing approaches offer measurable results:
Lean method:
- Waste elimination (muda)
- Continuous improvement (kaizen)
- Pull flow (just-in-time)
- Intermediate inventory reduction
5S system:
- Seiri: Remove unnecessary items
- Seiton: Organize efficiently
- Seiso: Clean regularly
- Seiketsu: Standardize practices
- Shitsuke: Maintain discipline
Typical gains achieved:
- Cycle time reduction
- Inventory decrease
- Quality improvement
4.2. Digitalization of work instructions with Picomto
Picomto revolutionizes production time optimization:
Key features:
- Interactive visual instructions
- Step-by-step operator guidance
- Complete operation traceability
- Real-time time analysis
Concrete advantages:
- Training time reduction
- Error decrease
- Productivity improvement
- Good practice standardization
4.3. Data analysis for continuous improvement
Intelligent data exploitation accelerates optimization:
- Automated collection: Sensors and industrial IoT
- Predictive analysis: Problem anticipation
- Dashboards: Performance visualization
- Proactive alerts: Quick reaction to deviations
Test our solution by requesting a personalized demo.
5. Which KPIs to monitor for managing your production times?
Effective production time management requires relevant and actionable indicators. Nevertheless, multiplying metrics can create confusion. Thus, we will identify essential KPIs and their optimal use.
5.1. Essential indicators to monitor
Unavoidable KPIs for production time tracking:
Overall Equipment Effectiveness (OEE):
- Formula: OEE = Availability × Performance × Quality
- Objective: Measure global efficiency
- Benchmark: 85% considered excellent
Cycle time:
- Duration between two finished products
- Production rate indicator
- Capacity calculation base
Downtime:
- Planned and unplanned breakdowns
- Changeovers
- Preventive maintenance
5.2. How to analyze and interpret data?
Data analysis requires a structured approach:
Analysis techniques:
- Pareto analysis: Identify 20% of causes creating 80% of problems
- Trend analysis: Performance evolution over time
- Comparative analysis: Benchmarking between lines or teams
Monitoring frequency:
- Daily: Immediate reactivity
- Weekly: Trend analysis
- Monthly: Review and planning
5.3. Effective dashboards with Picomto
Picomto offers intuitive and customizable dashboards:
Advanced features:
- Real-time visualization
- Automatic alerts
- Comparative analysis
- Automated reports
Specialized modules:
- Performance tracking by operator
- Time analysis by workstation
- Bottleneck identification
- Maintenance forecasting
5. Quels KPIs suivre pour piloter ses temps de production ?
Le pilotage efficace des temps de production nécessite des indicateurs pertinents et actionables. Néanmoins, la multiplication des métriques peut créer de la confusion. Ainsi, nous identifierons les KPIs essentiels et leur utilisation optimale.
5.1. Les indicateurs essentiels à surveiller
Les KPIs incontournables pour le suivi des temps de production :
Taux de Rendement Synthétique (TRS) :
- Formule : TRS = Disponibilité × Performance × Qualité
- Objectif : Mesurer l’efficacité globale
- Benchmark : 85% considéré comme excellent
Temps de cycle :
- Durée entre deux produits finis
- Indicateur de cadence de production
- Base de calcul de la capacité
Temps d’arrêt :
- Pannes planifiées et non planifiées
- Changements de série
- Maintenance préventive
5.2. Comment analyser et interpréter les données ?
L’analyse des données requiert une approche structurée :
Techniques d’analyse :
- Analyse de Pareto : Identifier les 20% de causes créant 80% des problèmes
- Analyse de tendance : Évolution des performances dans le temps
- Analyse comparative : Benchmarking entre lignes ou équipes
Fréquence de suivi :
- Quotidienne : Réactivité immédiate
- Hebdomadaire : Analyse des tendances
- Mensuelle : Bilan et planification
5.3. Les tableaux de bord efficaces avec Picomto
Picomto propose des tableaux de bord intuitifs et personnalisables :
Caractéristiques avancées :
- Visualisation en temps réel
- Alertes automatiques
- Analyse comparative
- Rapports automatisés
Modules spécialisés :
- Suivi des performances par opérateur
- Analyse des temps par poste
- Identification des goulots d’étranglement
- Prévision des maintenances
Conclusion
Production time optimization represents a major strategic challenge for manufacturing companies. Indeed, this approach directly impacts profitability, competitiveness, and customer satisfaction. The methods presented in this guide offer concrete and measurable improvement levers.
Essential points to remember:
- Precise measurement constitutes the indispensable prerequisite
- Systemic approach maximizes gains
- Digitalization accelerates transformations
- KPI-driven management ensures sustainability
Consequently, start your optimization approach now. Picomto accompanies you in this transformation through its innovative solutions and recognized expertise.
Start your transformation today:
Book your free demo and discover how to reduce your production times!
FAQ
How to calculate production time?
Production time = Setup time + Execution time + Finalization time.
What is production time?
Total duration required to manufacture a product from start to completion.
What are the 4 types of production?
Unit production, batch production, mass production, and continuous production according to volumes.
What is manufacturing time?
Duration of raw material transformation operations into finished products.
What is the formula to calculate production?
Production = Rate × Operating time × Efficiency rate.
What is production lead time?
Total time between customer order and product delivery.
How to calculate productive time?
Productive time = Total time – Downtime – Unproductive time.
What is the DP coefficient?
Production Availability coefficient measuring industrial equipment efficiency.
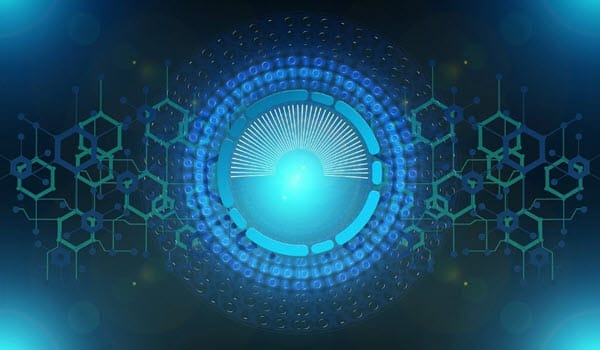
Leave A Comment