Notons que la performance industrielle ou le management de la performance se présente au cœur des préoccupations des grandes industries de production. La priorité est de viser l’excellence opérationnelle. Le but premier est de réduire au maximum sans pour autant diminuer la qualité de production afin de garantir le bon niveau de compétitivité.
La méthode Kaizen continue de nos jours de faire l’objet d’études et d’applications dans les industries du monde entier (automobile, aéronautique, agroalimentaire, luxe…). Initiée au Japon, ce système de management a su, par la suite, séduire les entreprises occidentales par l’approche unique qu’elle a de la production, des procédés, et du management. Consacrant l’amélioration continue, le système Kaizen est l’un des fondements du Lean manufacturing ou du Lean Management. Il propose des changements progressifs à tous les niveaux de l’organisation avec des méthodes et outils d’amélioration continue pour assurer un véritable pilotage de la performance industrielle et tendre vers l’excellence au niveau de la gestion industrielle.
Sommaire :
- La nécessité de s’améliorer pour exister
- L’amélioration continueau service de la performance industrielle
- Le Kaizen en tant que solution contre la résistance au changement
- La mesure des résultats de l’approche Kaizen
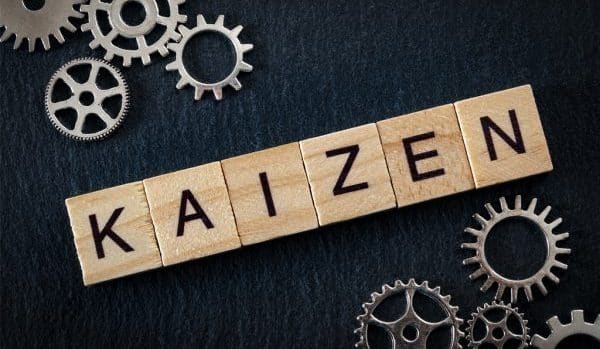
La performance industrielle, qu’est-ce que c’est ?
La performance industrielle se rapporte à l’efficacité, à la productivité et à l’ensemble des processus industriels. Évaluer cette performance aide les entreprises à repérer les axes d’amélioration, à affiner leurs opérations et à prendre des décisions basées sur des données fiables. Cela leur permet d’accroître leur productivité, leur rentabilité et d’atteindre l’excellence opérationnelle recherchée.
Les principaux indicateurs de la performance industrielle
Avant d’initier toute démarche d’amélioration de votre performance industrielle, il est essentiel d’évaluer votre situation actuelle pour identifier les axes prioritaires à travailler.
Pour cela, vous pouvez vous appuyer sur divers indicateurs clés de production qui garantissent l’amélioration continue du cycle de production.
Bien qu’ils varient selon le secteur et l’entreprise, voici sept indicateurs parmi les plus couramment utilisés :
TRS (Taux de Rendement Synthétique)
Cet indicateur évalue le temps réellement productif d’une machine ou d’une ligne de production par rapport au temps total disponible. Il permet ainsi de quantifier l’efficacité de la production et d’identifier les sources de pertes de temps.
Taux d’accidents du travail
Un taux élevé peut indiquer un non-respect des consignes de sécurité ou des cadences de travail excessives.
Taux d’heures supplémentaires
À l’exception des périodes de forte demande, un taux élevé d’heures supplémentaires peut signaler un effectif insuffisant ou mal réparti.
Taux de rebut
Cet indicateur permet d’identifier les processus qui posent des problèmes en matière de qualité de fabrication.
Capacité de production inutilisée
Cet indicateur aide à évaluer la capacité de l’entreprise à gérer des commandes supplémentaires ou à déterminer si des efforts commerciaux sont nécessaires pour optimiser la production.
Délais de livraison
Ce délai mesure le temps écoulé entre la commande du client et la livraison. Les délais de livraison, tout comme la qualité, sont cruciaux pour la satisfaction client. Il est donc essentiel de respecter les délais annoncés, tout en évaluant l’efficacité des opérations logistiques.
Kaizen : parce que stagner signifie reculer
Dans l’actuel contexte que l’on sait hautement concurrentiel, se contenter de son statut et de sa position actuelle, c’est condamner son entreprise au recul. Ne pas s’améliorer, c’est forcément perdre du terrain par rapport aux concurrents qui, eux, s’efforcent de développer leurs capacités à différents niveaux.
La méthode Kaizen, qui prône l’amélioration continue, répond à cette nécessité d’évolution permanente dans le secteur industriel. D’ailleurs, plus qu’une méthode, elle est associée à une véritable culture d’entreprise. Elle vise notamment à apporter une mentalité tout autre, et ce, des postes décisionnels jusqu’à dans les ateliers et les sites de production.
Kaizen : Pour une performance industrielle soutenue
Il faut savoir, tout d’abord, que la performance industrielle a pour but premier d’optimiser les fonctions opérationnelles des entreprises en suivant entre autres un modèle d’industrie 4.0.
Dans une entreprise organisée selon les principes du Kaizen, les changements se font par petites doses et à un rythme continu (quotidiennement) pour assurer l’amélioration continue et une meilleure résolution de problèmes opérationnels. Les opérations d’amélioration se doivent également d’être simples, peu coûteuses et tangibles. C’est une approche diamétralement opposée à celles basées sur les révisions de grande ampleur, les ruptures rapides et de fond qui peuvent présenter d’importants risques (difficulté d’acceptation et d’assimilation par les collaborateurs notamment).
La méthode Kaizen se caractérise aussi par le fait qu’elle implique l’ensemble des acteurs de l’entreprise dans le domaine industriel. Cette méthode n’implique pas seulement le management (le responsable de production industrielle, le responsable méthodes, le responsable maintenance industrielle le responsable de chaîne logistique, l’ingénieur généraliste, responsable amélioration continue, ingénieur en génie mécanique, ou chef de projet industrialisation). De l’opérationnel à la direction, chaque employé est incité à analyser son propre poste de travail et à y identifier les opportunités d’amélioration. La motivation et l’engagement font, en effet, partie des aspects primordiaux du principe d’amélioration continue Kaizen. Notons que le bureau des méthodes, étant l’interface entre la production et le bureau d’études, il est en mesure de garantir le bon déroulement des processus industriels.
D’autre part, mettre en place un logiciel d’ordonnancement de la production est en mesure d’améliorer la performance industrielle d’une usine du futur, et ce, peu importe le secteur d’activité.
De manière globale, ce dernier se place au service de la performance industrielle en :
- Visant à améliorer des performances industrielles : la qualité et les délais de production
- Optimisant la gestion des flux, la gestion des stocks, la gestion des systèmes de production, Elimination des gaspillages
- Renforçant la productivité
- Organisant les lignes de production et en régulation les flux (gestion de production)
- Améliorant l’environnement de travail
- Eliminant le gaspillage (la non valeur ajoutée)
La meilleure définition que l’on puisse donner de cette démarche d’amélioration continue est celle de Masaaki Imai, fondateur du Kaizen Institute : « Everyday improvement, everybody improvement and everywhere improvement » (l’amélioration tous les jours, de la part de tout le monde et partout).
Une parade efficace à la résistance au changement ?
Le phénomène de résistance au changement existe partout et dans tous les secteurs dans le milieu industriel. Les managers y sont souvent confrontés et la mise en œuvre de leurs mesures amélioratrices est donc complexe, voire impossible dans certains cas.
L’un des avantages de l’approche Kaizen, c’est que les changements qu’elle invite à effectuer sont mieux acceptés par le personnel, en raison de leur caractère progressif et doux. Ce qui rejoint l’idée que les collaborateurs se sentent, par conséquent, plus impliqués dans le projet. Et des équipes plus concernées par le développement de leur entreprise sont, de facto, plus performantes.
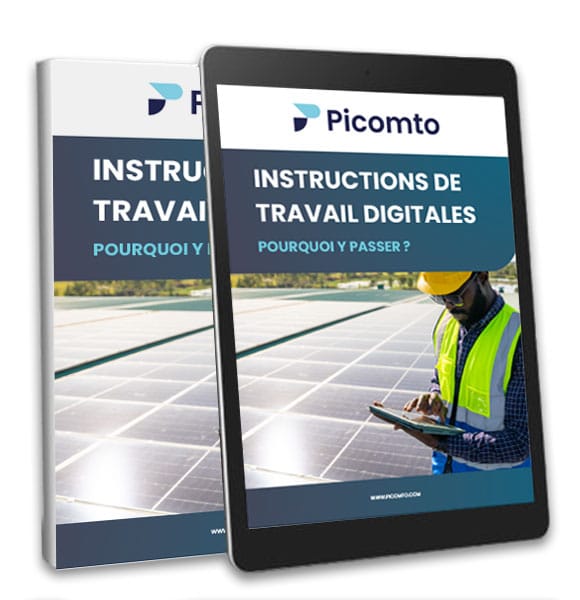
voyages évités chaque semaine
gagnés chaque année
Quelles sont les autres méthodes et outils pour mesurer la performance industrielle ?
Le lean management propose plusieurs méthodes supplémentaires pour évaluer la performance industrielle et améliorer les fonctions opérationnelles des entreprises.
- L’audit 5S (seiri, seiton, seiso, seiketsu, shitsuke) permet d’organiser l’espace de travail, de minimiser les temps de recherche et d’optimiser les flux de production.
- Le diagramme d’Ishikawa, aussi appelé diagramme de causes et effets, facilite l’identification des origines des problèmes et aide à développer des solutions adaptées.
Utiliser des outils digitaux et logiciels de gestion adaptés
À l’ère de la quatrième révolution industrielle, les nouvelles technologies sont des atouts essentiels pour améliorer le pilotage de la performance dans le secteur industriel.
L’intelligence artificielle et les outils numériques permettent d’optimiser et d’accélérer l’ensemble des cycles de production. Ils permettent de :
- Faciliter la détection des anomalies en temps réel,
- Renforcer la gestion des risques opérationnels (tels que les retards de livraison, le vieillissement des équipements et les pannes de machines)
- et simplifier le partage de l’information à tous les niveaux de l’entreprise.
La digitalisation de la chaîne de production contribue ainsi à :
- optimiser le pilotage des flux,
- rationaliser les ressources
- et faire gagner un temps précieux aux équipes opérationnelles.
Voici quelques exemples d’outils numériques dédiés à la performance industrielle :
- Logiciels de gestion de la production : MES (Manufacturing Execution System), WMS (Warehouse Management System), ERP (Enterprise Resource Planning)
- L’IoT (Internet des Objets)
- L’utilisation du Big Data
- Objets connectés
- Automatisation robotisée des processus
- Outils d’intelligence artificielle (IA)
- Réalité augmentée (AR) et réalité virtuelle (VR)
Mesurez l’impact de vos initiatives Kaizen avec Picomto. Inscrivez-vous à notre webinar pour en savoir plus.
Picomto : outil d’amélioration continue de la performance industrielle
Chez Picomto, nous développons un logiciel d’instructions de travail digitales qui participe grandement au processus d’amélioration continue dans les usines et les entreprises industrielles en facilitant la récolte de données dans les ateliers. Les opérateurs contribuent à alimenter les processus pour établir des plans d’action et ainsi favoriser l’excellence opérationnelle et la productivité. Il sert également à mettre en œuvre une démarche de management visuel et piloter la performance opérationnelle pour l’optimisation et l’amélioration de la performance et booster la compétitivité de l’entreprise dans le contexte de l’industrie du futur ou la digitalisation est le mot d’ordre.
Vous voulez en savoir plus ? Contactez nos experts métier qui seront ravis d’échanger autour de vos problématiques.
FAQ
Performance industrielle : quels objectifs ?
L’objectif principal de la performance industrielle est d’optimiser les fonctions opérationnelles tout en réduisant les coûts afin d’augmenter la rentabilité. Il s’agit d’améliorer la performance sans compromettre la qualité de la production et des conditions de travail, afin de rester compétitif sur le marché.
Performance industrielle : pour quel type d’entreprise ?
Toutes les entreprises, quelle que soit leur taille ou leur secteur d’activité, peuvent bénéficier de la performance industrielle. Ce concept peut être mis en œuvre sans nécessiter une organisation complexe ou des investissements initiaux importants. Ainsi, la performance industrielle peut être développée en interne pour améliorer les résultats, notamment par le biais d’une culture axée sur l’excellence opérationnelle.
Quels sont les 4 types d’indicateurs clés de la performance industrielle ?
Divers types d’indicateurs peuvent être utilisés pour évaluer la performance industrielle des entreprises manufacturières :
- Indicateurs de productivité
- Indicateurs de coûts
- Indicateurs de processus
- Indicateurs humains
Quels sont les avantages d’un audit de performance industrielle ?
Un audit permet d’identifier les points faibles, de mesurer l’efficacité des processus, et de formuler des recommandations d’amélioration.
Quels sont les impacts de la performance industrielle sur la satisfaction client ?
Une meilleure performance industrielle se traduit souvent par une amélioration de la qualité, des délais de livraison respectés, et une augmentation de la satisfaction client.
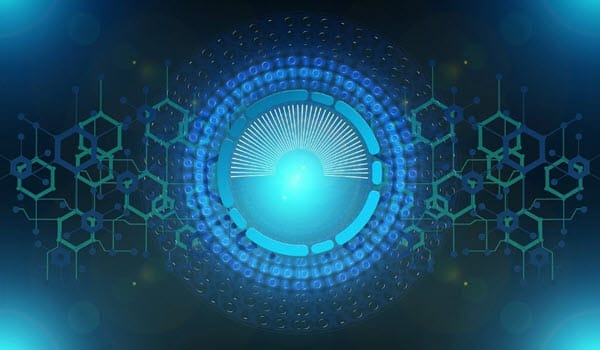
Laisser un commentaire