Face aux défis industriels actuels, la méthode Kaizen s’impose comme une solution incontournable. Cette approche japonaise d’amélioration continue a permis aux entreprises de réduire leurs coûts de 20-30% dès la première année tout en augmentant leur productivité de 30%. Contrairement aux révolutions coûteuses, le Kaizen mise sur des petits changements quotidiens impliquant chaque collaborateur. À l’ère de l’Industrie 4.0, sa digitalisation démultiplie son impact avec des résultats 40% plus rapides. Découvrez comment implémenter cette méthode éprouvée et transformer durablement votre performance industrielle.
Points Clés à Retenir concernant la méthode Kaizen :
- La méthode Kaizen vise l’amélioration continue par petits pas
- Réduction moyenne des coûts de 20-30% la première année
- Applicable dans tous les secteurs industriels
- Combinaison efficace avec les outils digitaux
- Plus de 80% des entreprises du Fortune 500 l’utilisent
1. Qu’est-ce que la méthode kaizen et pourquoi est-elle incontournable dans l’industrie ?
Et si de petits changements pouvaient produire de grands résultats ?
C’est exactement ce que propose la méthode Kaizen, un pilier de l’amélioration continue en milieu industriel. Adoptée dans le monde entier, cette approche japonaise mise sur des améliorations progressives, régulières, mais surtout durables. Elle transforme la culture d’entreprise, renforce l’efficacité des processus et place chaque collaborateur au cœur du changement.
1.1. Aux origines de la méthode Kaizen : Une réponse au défi industriel japonais
La méthode Kaizen est née dans un contexte de crise. Au lendemain de la Seconde Guerre mondiale, le Japon devait reconstruire son industrie avec des moyens limités. C’est dans ce climat que Taiichi Ohno, ingénieur chez Toyota, met au point une méthode basée sur l’efficience, la rigueur et l’intelligence collective.
Résultat ? En seulement cinq ans, Toyota réduit ses coûts de production de 50 %.
Un exploit qui inspire très vite les entreprises du monde entier.
1.2. Les 5 principes clés de la méthode Kaizen
La force du Kaizen repose sur des piliers simples, mais puissants :
- Amélioration continue : chaque jour est une opportunité pour faire mieux.
- Implication de tous les collaborateurs : du technicien à la direction, chacun a un rôle à jouer.
- Élimination des gaspillages (muda) : temps, énergie, matière… rien ne doit être perdu.
- Standardisation des processus : pour garantir la qualité et la reproductibilité.
- Management visuel : pour rendre les informations claires, visibles et partagées par tous.
2. Comment Mettre en Place la méthode kaizen dans votre entreprise industrielle ?
Envie d’améliorer vos performances sans bouleverser toute votre organisation ?
La méthode Kaizen est la réponse. Mais sa mise en œuvre demande méthode, rigueur et engagement collectif.
Les entreprises les plus performantes suivent un processus structuré, étape par étape. C’est la clé d’un déploiement réussi et durable.
2.1. Quelles sont les étapes clés du déploiement du Kaizen ?
Tout commence par un diagnostic précis.
Étape 1 : Évaluation initiale – identifiez les zones à fort potentiel d’amélioration.
Étape 2 : Formation des équipes – expliquez les concepts, impliquez chaque niveau hiérarchique.
Étape 3 : Déploiement progressif – lancez des actions concrètes, évaluez, ajustez, puis étendez.
Les chiffres parlent d’eux-mêmes : +25 % de productivité en moyenne chez les entreprises engagées dans une démarche Kaizen bien structurée.
2.2. Comment identifier les zones d’amélioration prioritaires ?
Pas besoin d’attendre une crise pour agir. L’analyse des processus en place révèle souvent des gaspillages invisibles mais coûteux.
- Le Gemba Walk – allez sur le terrain, observez sans filtre.
- Le diagramme d’Ishikawa – mettez en lumière les causes profondes d’un problème.
Exemple concret : Veolia a réduit de 30 % ses gaspillages grâce à cette approche.
En digitalisant ses processus, elle a pu accélérer les actions correctives et renforcer l’adhésion des équipes.
2.3. Quels sont les outils essentiels du Kaizen ?
Le Kaizen n’est pas une idée abstraite. Il s’appuie sur des outils concrets, faciles à mettre en œuvre sur le terrain :
- Les 5S – pour organiser efficacement l’espace de travail
- Le PDCA – pour structurer la résolution de problèmes
- Le Kanban – pour mieux gérer les flux de production
- Le management visuel – pour rendre les informations visibles et partagées
- Les standards de travail – pour garantir la qualité et la reproductibilité
3. Comment digitaliser efficacement votre démarche Kaizen ?
Le Kaizen est puissant. Mais avec le digital, il devient redoutablement efficace.
Grâce à la digitalisation, les entreprises identifient plus vite les problèmes, suivent leurs actions en temps réel, et déploient les bonnes pratiques sans délai.
Résultat : des gains de productivité visibles et durables.
3.1. Pourquoi la digitalisation est-elle devenue incontournable pour le Kaizen moderne ?
Aujourd’hui, impossible de parler d’amélioration continue sans parler de technologie.
Les entreprises qui digitalisent leur démarche Kaizen enregistrent jusqu’à 40 % de résultats supérieurs.
Pourquoi ? Parce que les données sont centralisées, les retours du terrain sont instantanés, et l’analyse devient plus rapide.
Exemple concret : Daher a réduit de 50 % ses temps de formation en digitalisant ses standards de travail et ses procédures.
3.2. Comment les solutions digitales boostent l’efficacité du Kaizen ?
Les outils numériques ne remplacent pas le Kaizen. Ils le renforcent. Prenons Picomto : une solution pensée pour l’industrie, centrée sur la simplicité et l’agilité.
Voici ce qu’elle permet :
- Capture instantanée des suggestions du terrain
- Analyse en temps réel des indicateurs de performance
- Partage immédiat des bonnes pratiques à l’échelle de l’entreprise
- Suivi précis des actions engagées
- Formation continue grâce à des supports accessibles et interactifs
4. Quels résultats concrets attendre de la digitalisation du Kaizen ?
Les entreprises qui digitalisent leur Kaizen obtiennent des résultats impressionnants. Les chiffres parlent d’eux-mêmes.
- Réduction des temps de formation : -50%
- Augmentation de la productivité : +30%
- Diminution des erreurs : -65%
- Amélioration de la qualité : +40%
4.1. Quels sont les impacts mesurables du kaiezn sur la performance industrielle ?
Le Kaizen, ce n’est pas seulement une philosophie.
C’est une source de résultats concrets, visibles sur le terrain.
- Réduction des coûts
- Amélioration de la qualité
- Hausse de la productivité
- Meilleure satisfaction client
Bref, une transformation globale, mesurable à chaque étape.
4.2. Comment le Kaizen améliore-t-il la productivité ?
Le gain de productivité est souvent le premier indicateur à progresser. En moyenne, les entreprises observent une hausse de 25 à 35 % de leur productivité.
Exemple frappant : Butachimie a augmenté sa productivité de 40 % en un an, tout en réduisant ses coûts de maintenance de 30 %.
Une double performance, rendue possible grâce à une démarche Kaizen structurée.
4.3. Quel est l’impact sur la qualité et la satisfaction client ?
Avec le Kaizen, la qualité s’améliore naturellement.
- Moins d’erreurs.
- Moins de défauts.
- En moyenne, les défauts sont réduits de 50 %.
Et cela se reflète directement sur la satisfaction client.
Les études montrent une hausse moyenne de 45 % des indicateurs de satisfaction (NPS, feedbacks, taux de réclamation…).
4.4. Comment Mesurer le ROI de Votre Démarche Kaizen ?
Un des grands avantages du Kaizen, c’est sa mesurabilité. Chaque action menée peut être évaluée avec des KPI concrets.
Voici les indicateurs les plus utilisés :
- Taux de productivité
- Réduction des coûts opérationnels
- Baisse du taux de défauts
- Amélioration de la satisfaction client
- Hausse de l’engagement des équipes
5. Comment assurer la pérennité de votre démarche Kaizen ?
Mettre en place le Kaizen, c’est bien. Mais le vrai défi, c’est de le faire durer dans le temps.
Les entreprises qui réussissent savent que l’amélioration continue ne s’improvise pas. Elle repose sur des pratiques solides, partagées et soutenues à tous les niveaux.
5.1. Quels sont les facteurs clés de succès à long terme ?
Le Kaizen ne tient pas tout seul. Il s’ancre durablement grâce à cinq leviers essentiels :
- Un engagement fort de la direction – sans impulsion claire, pas de dynamique durable
- Une formation continue – les compétences doivent évoluer en même temps que les processus
- Une communication transparente – les objectifs et les résultats doivent être visibles et compris
- Une célébration des succès – chaque amélioration, même minime, mérite d’être reconnue
- Une adaptation constante – le Kaizen doit s’ajuster aux nouveaux enjeux et aux retours terrain
- Une digitalisation progressive – pour faciliter le suivi, le partage et la capitalisation des bonnes pratiques
5.2. Comment maintenir la motivation des équipes ?
Un Kaizen sans équipes engagées, c’est une coquille vide. La motivation ne se décrète pas, elle se cultive. Les entreprises performantes misent sur la reconnaissance, l’autonomie et la participation active.
Cas inspirant : la Marine Nationale a réussi à augmenter l’engagement de ses équipes de 60 %.
Leur secret ? Une stratégie de digitalisation bien pensée, qui a rendu visibles les efforts de chacun et simplifié la transmission des savoirs.
Conclusion
La méthode Kaizen révolutionne l’industrie depuis plus de 50 ans.
Sa combinaison avec les outils digitaux démultiplie son efficacité. Les entreprises qui l’adoptent constatent des améliorations significatives. La digitalisation accélère ces transformations.
FAQ
Q: Quel est le principe du Kaizen ?
R: Le Kaizen vise l’amélioration continue par petits changements quotidiens impliquant tous les employés.
Q: Quelles sont les quatre étapes de la méthode Kaizen ?
R: Plan (Planifier), Do (Faire), Check (Vérifier), Act (Agir). Ce cycle PDCA structure toute démarche d’amélioration.
Q: Quels sont les 5 dans Kaizen ?
R: Les 5M : Main d’œuvre, Matière, Matériel, Méthode, Milieu. Ils guident l’analyse des problèmes.
Q: C’est quoi le 5S Kaizen ?
R: Seiri (Trier), Seiton (Ranger), Seiso (Nettoyer), Seiketsu (Standardiser), Shitsuke (Maintenir). Ils organisent l’espace de travail.
Q: Quel est l’outil de base du Kaizen ?
R: Le Gemba Walk permet d’observer directement les processus sur le terrain pour identifier les améliorations.
Q: Quel est l’objectif du Kaizen ?
R: Éliminer les gaspillages, améliorer la qualité et augmenter la productivité par des actions continues.
Q: Quelles sont les 10 règles du Kaizen ?
R: 1. Éliminer les gaspillages 2. Améliorer en continu 3. Impliquer tous les employés 4. Favoriser les petits changements 5. Agir sur le terrain 6. Standardiser les pratiques 7. Utiliser le management visuel 8. Prendre des décisions sur faits 9. Prévenir plutôt que corriger 10. Pérenniser les améliorations
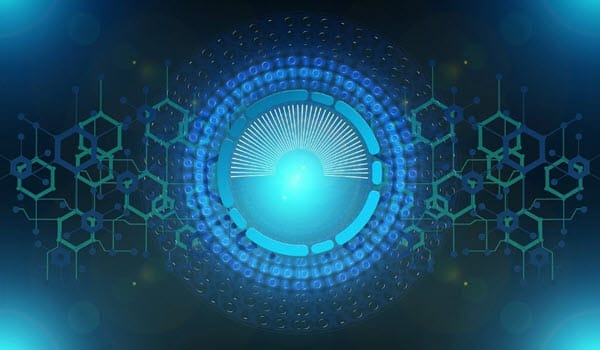
Laisser un commentaire